Na manutenção, o modo de falha é a forma como um defeito se apresenta no equipamento, ou seja, o sinal apresentado quando o maquinário em questão deixa de desempenhar sua função.
A seguir, entenda o que é o modo de falha e análise FMEA, sua importância, e veja como a tecnologia pode te ajudar nesse processo. Boa leitura!
Veja também: Relatório de não conformidade digital para registrar modos de falha
O que é modo de falha?
O termo modo de falha se refere a todas as maneiras que um equipamento deixa de funcionar ou não atende aos requisitos especificados. Em outras palavras, é a forma como algo deixa de desempenhar a função para a qual foi projetado.
Por exemplo: um sistema de combate a incêndio pode apresentar diferentes modos de falha, tais como baterias fracas, problemas na fiação, falhas no detector ou no emissor do alarme, defeitos na ativação dos sprinklers, entre outros.
Ou seja, esses são alguns exemplos de possíveis modos de falha apresentados por um sistema de combate a incêndio.
Os modos de falha variam dependendo do contexto. Eles podem ser divididos em categorias, como falhas mecânicas, elétricas, químicas, entre outras, dependendo do tipo de sistema ou equipamento em questão. Identificar e analisar os modos de falha é fundamental para o desenvolvimento de estratégias eficazes de prevenção de falhas, tipos de manutenção adequados e melhoria da confiabilidade dos ativos.
Além disso, os modos de falha são frequentemente avaliados por meio de análises de modos de falha e efeitos (FMEA) ou análises de árvores de falha (FTA). Essas abordagens ajudam a entender as possíveis causas de falhas, as consequências associadas e a priorizar as ações de mitigação com base nos riscos identificados.
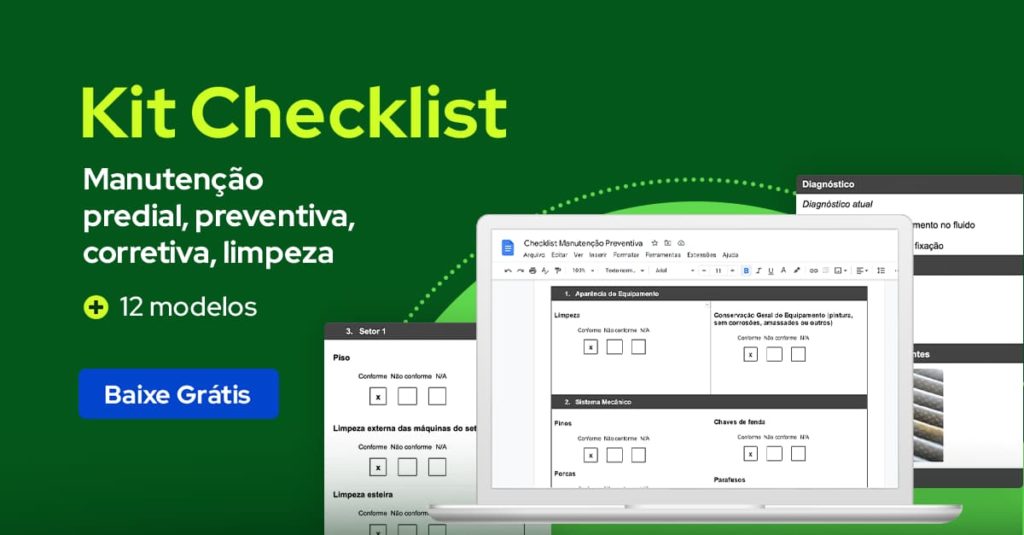
O que é a análise de modo e efeito de falha?
A Análise de Modo e Efeito de Falha (FMEA, do inglês Failure Modes and Effects Analysis) é uma metodologia usada para identificar e avaliar potenciais modos de falha em um equipamento, bem como analisar as consequências dessas falhas.
O objetivo principal da FMEA é melhorar a confiabilidade, a segurança e o desempenho dos ativos ao identificar e mitigar as falhas potenciais antes que elas ocorram.
A análise FMEA geralmente é realizada em equipes multidisciplinares que incluem especialistas em diferentes áreas, como engenharia, produção, manutenção e qualidade. O processo envolve as seguintes etapas:
- Identificação dos modos de falha (Failure Modes): a equipe identifica todas as possíveis maneiras pelas quais o equipamento, sistema ou processo pode falhar. São os modos de falha, como citamos anteriormente;
- Análise dos efeitos das falhas (Effects Analysis): para cada modo de falha identificado, a equipe analisa os efeitos potenciais dessas falhas no equipamento. Os efeitos podem variar em termos de gravidade, desde inconvenientes menores até consequências sérias;
- Avaliação da severidade, ocorrência e detecção (Risk Assessment): cada modo de falha é avaliado quanto à sua severidade (gravidade dos efeitos), ocorrência (probabilidade de ocorrer) e detecção (probabilidade de detecção antes que a falha cause um efeito). Esses três fatores são usados para calcular um índice de risco, conhecido como Prioridade de Risco;
- Desenvolvimento de ações de mitigação: com base na avaliação do risco, a equipe propõe ações de prevenção e controle para reduzir ou eliminar os modos de falha de maior risco;
- Implementação das ações e monitoramento: as ações de mitigação são implementadas e o processo é monitorado ao longo do tempo para garantir que as melhorias esperadas sejam alcançadas. Se necessário, são feitas alterações nos planos de ação.
A FMEA é uma ferramenta muito importante para aprimorar a confiabilidade e a qualidade dos equipamentos e processos, identificando áreas de potencial melhoria e direcionando os recursos para as questões mais críticas. Essa análise é comumente usada em setores de alta criticidade, como a indústria automotiva, aeroespacial, área da saúde e muitos outros onde a prevenção de falhas é crucial.
Qual a relação do modo de falha com a FMEA?
Como vimos logo acima, o modo de falha é uma parte fundamental da FMEA, já que é a primeira etapa da análise. Enquanto o modo de falha refere-se à forma como um equipamento pode deixar de cumprir sua função prevista, a FMEA identifica, analisa e prevê esses modos de falha, proporcionando uma abordagem preventiva para evitar o surgimento de problemas.
A FMEA é conduzida em várias etapas, e a identificação dos modos de falha é uma das primeiras fases do processo. Durante a análise dos modos de falha, a equipe trabalha para listar todos os possíveis modos de falha que podem ocorrer no ativo em questão. Esses modos de falha podem incluir falhas mecânicas, elétricas, térmicas, de software, entre outras, dependendo do contexto.
Leia também: Inspeção termográfica: o que é, importância e como realizar
Após identificar os modos de falha, a análise continua avaliando os efeitos dessas falhas (Análise de Efeito de Falha), a probabilidade de ocorrência de cada modo de falha e a probabilidade de detecção antes que a falha cause um efeito indesejado. Essa avaliação é realizada para cada modo de falha identificado.
A FMEA utiliza os modos de falha como ponto de partida para analisar as consequências potenciais, avaliar o risco associado e desenvolver estratégias de prevenção e controle, minimizando os riscos de falha.
Qual a relação do modo de falha com a FMECA?
Além da FMEA, o modo de falha está relacionado a outra análise, a Análise dos Modos de Falha, Efeito e Criticidade (FMECA, ou Failure Mode, Effects, and Criticality Analysis).
A FMECA é uma extensão da FMEA que adiciona uma dimensão extra à análise. Ambas são ferramentas de análise de risco utilizadas para identificar e minimizar modos de falha em máquinas e equipamentos.
A FMECA inclui três componentes principais:
- Análise de modo de falha (Failure Mode Analysis): esta fase é semelhante à primeira etapa da FMEA, na qual os modos de falha potenciais são identificados. Cada modo de falha é descrito em termos de como ele pode ocorrer e como ele pode afetar o ativo ou sistema;
- Análise de efeito de falha (Effect Analysis): assim como a análise de efeito de falha na FMEA, as possíveis consequências de cada modo de falha são avaliadas em termos de gravidade;
- Análise de criticidade (Criticality Analysis): esta é a principal diferença da FMECA em relação à FMEA. Na análise de criticidade, os modos de falha são avaliados em termos de sua criticidade, levando em consideração não apenas a gravidade dos efeitos, mas também a importância do equipamento para a produção, a probabilidade de ocorrência e a capacidade de detecção antes que a falha cause danos. O resultado é uma avaliação mais completa do risco, incorporando diferentes dimensões.
Leia também: Matriz de Criticidade: o que é e como implementar?
Portanto, tanto a FMEA quanto a FMECA utilizam a análise dos modos de falha como ponto de partida, sendo que a FMECA acrescenta uma avaliação mais aprofundada da criticidade dos modos de falha. Essa análise de criticidade pode ser usada para priorizar ações de prevenção e direcionamento de recursos, concentrando-se nos modos de falha mais críticos e com maior potencial de impacto adverso.
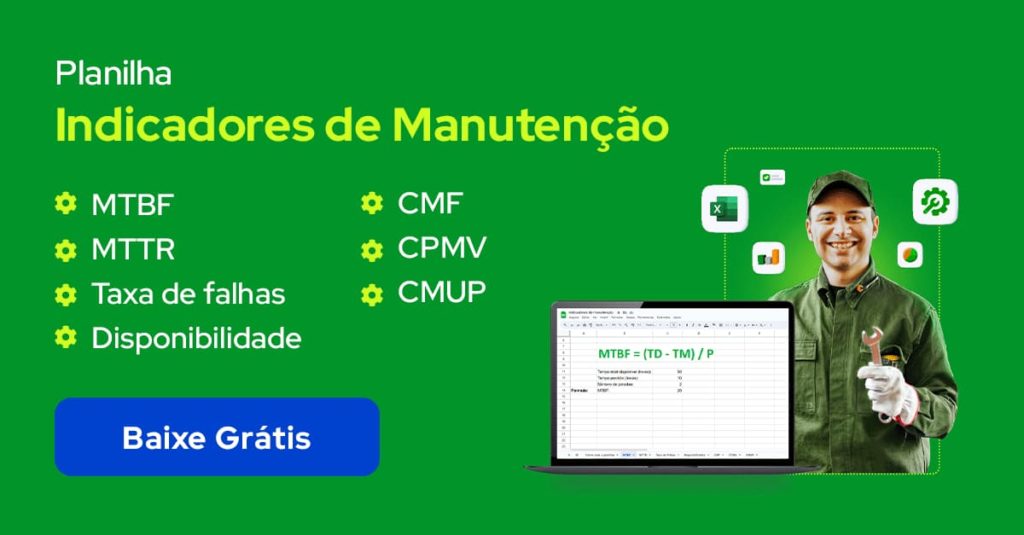
Por que é importante conhecer o modo de falha?
Conhecer os modos de falha é fundamental em vários campos, especialmente em engenharia, manutenção, qualidade e gestão de riscos. Aqui estão algumas razões pelas quais é importante conhecer os modos de falha:
- Prevenção de falhas: compreender como o equipamento pode falhar permite que os profissionais adotem medidas proativas para prevenir essas falhas. Isso inclui melhorias no design, implementação de práticas de manutenção preventiva e correção de possíveis pontos fracos, mesmo que estes não tenham causado problemas ainda;
- Melhoria da confiabilidade: ao identificar e abordar os modos de falha potenciais, é possível aumentar a confiabilidade do equipamento. Isso é crucial em segmentos onde a confiabilidade é essencial, como na aviação, na indústria automotiva, em equipamentos médicos e em sistemas críticos de infraestrutura;
- Redução de custos: conhecer os modos de falha permite implementar estratégias de manutenção mais eficientes e econômicas. A manutenção preventiva baseada em riscos, focada nos modos de falha mais críticos, ajuda a reduzir custos operacionais e evitar interrupções não planejadas;
- Garantia da qualidade: em linhas de produção, a compreensão dos modos de falha ajuda a garantir a qualidade do produto final, já que a detecção precoce e a prevenção de falhas contribuem para produtos mais confiáveis e duráveis;
- Segurança: em muitos casos, os modos de falha podem estar relacionados a questões de segurança do trabalho. Conhecer esses modos de falha é crucial para garantir a segurança dos colaboradores que operam o equipamento, dos usuários e do público em geral. Isso é especialmente relevante em setores como o nuclear, o petroquímico e o de transporte;
- Gestão de riscos: a análise dos modos de falha é uma parte integrante da gestão de riscos. Identificar e avaliar os modos de falha ajuda na compreensão dos riscos associados a um ativo ou processo, permitindo a implementação de medidas apropriadas para evitar e controlar esses riscos;
- Melhoria contínua: a compreensão dos modos de falha é fundamental para processos de melhoria contínua. Ao analisar e corrigir os modos de falha, as empresas podem evoluir constantemente, aumentando a eficiência, a confiabilidade e a qualidade ao longo do tempo.
Em resumo, conhecer os modos de falha é essencial para tomar decisões informadas, melhorar a segurança dos sistemas, e garantir a qualidade e a eficiência contínuas.
Como fazer a análise do modo de falha?
A análise do modo de falha geralmente é realizada por meio de uma metodologia sistemática, como a Análise de Modo e Efeito de Falha (FMEA) ou a Análise de Modo de Falha, Efeito e Criticidade (FMECA).
Independentemente de qual metodologia será utilizada, separamos as principais etapas para você realizar a análise de modo de falha na sua empresa, olha só:
Formação da equipe
Monte uma equipe multidisciplinar composta por especialistas nas áreas relevantes. Isso pode incluir engenheiros, operadores, técnicos, especialistas em manutenção, qualidade, entre outros, dependendo do contexto.
Identificação dos modos de falha
Realize uma sessão de brainstorming para identificar todos os possíveis modos de falha que podem ocorrer no equipamento. Considere o histórico do ativo e todas as etapas do ciclo de vida, desde a concepção até o descarte.
Descrição dos modos de falha
Para cada modo de falha identificado, elabore uma descrição detalhada que inclua como o modo de falha pode ocorrer, quando ele pode ocorrer e quais são os seus efeitos no equipamento.
Análise dos efeitos das falhas
Avalie os efeitos potenciais de cada modo de falha. Isso envolve considerar a gravidade dos impactos e como esses impactos afetariam o desempenho, a segurança, a qualidade e outros aspectos relevantes do equipamento.
No caso de um sistema contra incêndio, por exemplo, alguns possíveis efeitos das falhas seriam alastramento do fogo e até explosão.
Leia também: Inspeção de extintores: como fazer e modelo pronto de ficha
Atribuição de severidade
Atribua uma pontuação de severidade para cada modo de falha por meio de uma escala numérica, em que valores mais altos indicam efeitos mais graves.
Identificação das causas dos modos de falha
Determine as possíveis causas subjacentes de cada modo de falha. Isso ajuda a entender a causa raiz das falhas e orienta a busca por soluções eficazes que resolvam a origem do problema, não apenas a forma como ele se apresenta.
Atribuição de probabilidade de ocorrência
Avalie a probabilidade de ocorrência de cada modo de falha. Novamente, isso geralmente é feito em uma escala numérica, em que valores mais altos indicam maior probabilidade da falha ocorrer.
Atribuição de probabilidade de detecção
Avalie a probabilidade de detecção de cada modo de falha antes que ele cause um efeito indesejado. Ou seja, caso a falha venha ocorrer, os mecanismos de detecção serão capazes de apontar o problema?
Voltando ao exemplo das falhas em sistemas contra incêndio, é possível que a falha só seja identificada quando o sistema não funcionar adequadamente em uma situação de emergência. Portanto, é preciso avaliar estratégias que ajudem a detectar a falha o quanto antes, como o cronograma de manutenção preventiva.
Essa atribuição também pode ser feita em escala numérica.
Cálculo da Prioridade de Risco
Calcule a Prioridade de Risco (Risk Priority Number, ou RPN) para cada modo de falha multiplicando as pontuações de severidade, probabilidade de ocorrência e probabilidade de detecção.
Quanto mais alto o número, maior é o risco e portanto mais crítica é a falha. Isso ajuda a priorizar os modos de falha com base no risco.
Desenvolvimento de ações de mitigação
Com base nas prioridades de risco, desenvolva ações de mitigação para reduzir ou eliminar os modos de falha. Estas podem incluir alterações no design, melhorias nos processos, implementação de sistemas de monitoramento, entre outras.
Implementação das ações
Coloque em prática as ações de mitigação desenvolvidas e acompanhe a eficácia ao longo do tempo. Faça inspeções periódicas para avaliar se as medidas implementadas estão sendo eficientes e, se necessário, faça alterações e novas implementações.
A análise do modo de falha é um processo contínuo, e deve ser revisada à medida que novas informações se tornam disponíveis ou quando há mudanças no equipamento em análise.
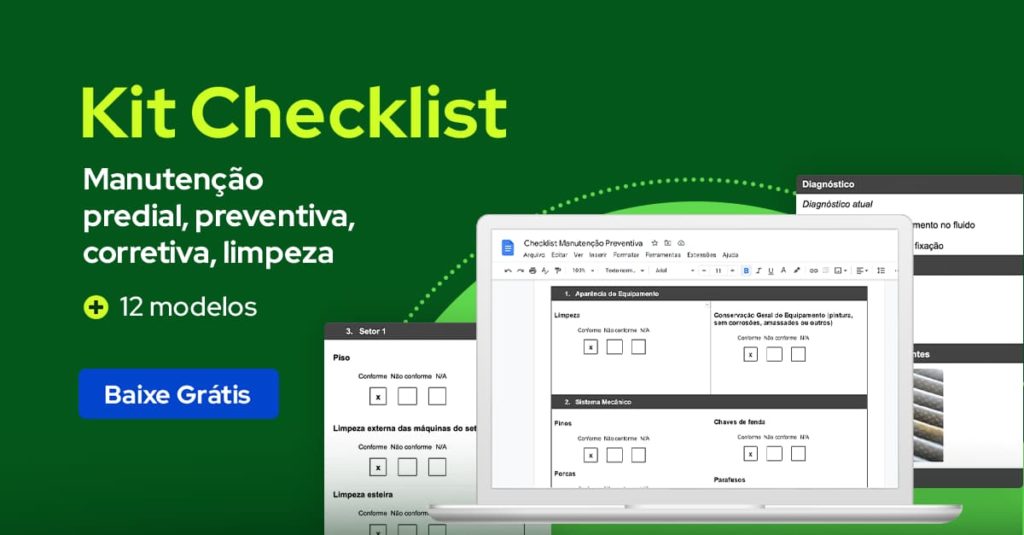
Como a tecnologia pode ajudar no controle do modo de falha?
A análise de modo de falha pode ser feita de forma manual no papel, mas com o uso da tecnologia, esse processo fica mais rápido e confiável. Para isso, você pode investir em um sistema como o Produttivo, que te ajuda a planejar, executar e controlar serviços de forma automatizada.
Com o Produttivo, é possível registrar os modos de falha por meio de relatórios digitais, como o Modelo Relatório de Não Conformidade. Ele foi especialmente desenvolvido para documentar as não conformidades encontradas no ativo, facilitando sua correção.
Vamos ver como fica o relatório de não conformidade digital preenchido e exportado em PDF:
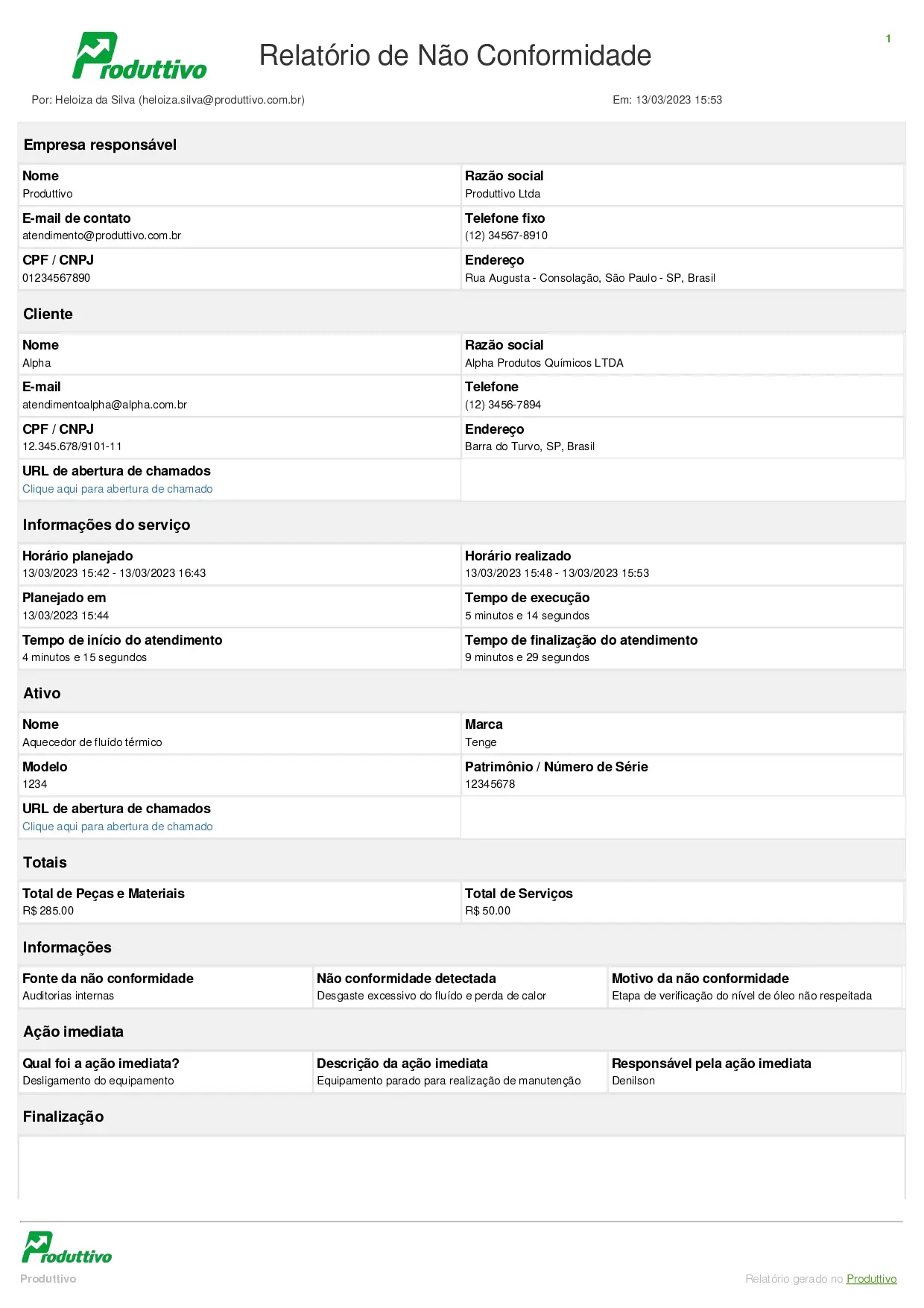
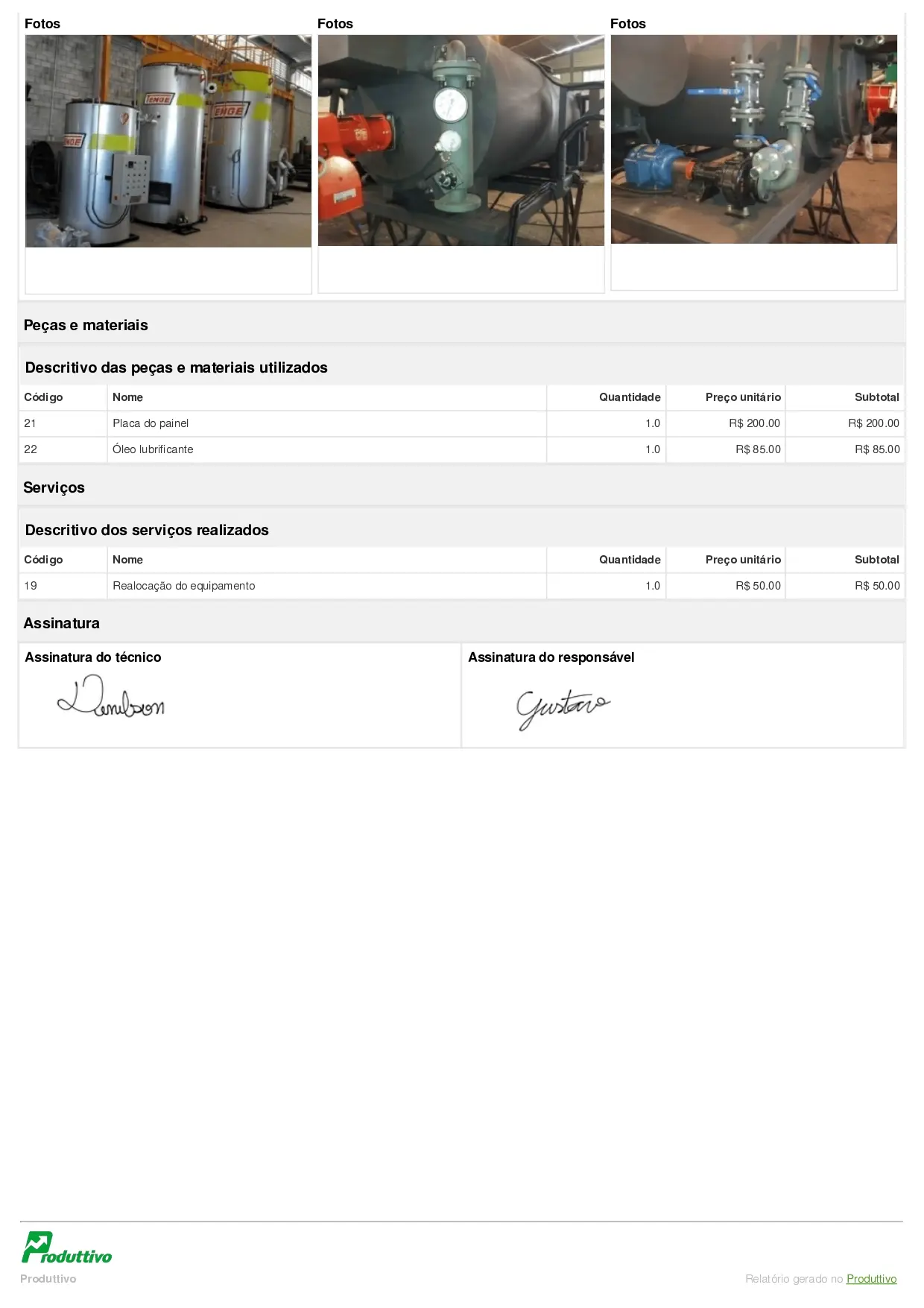
Para automatizar ainda mais sua operação, os relatórios inteligentes do Produttivo ainda contam com recursos como:
- Preenchimento automático do cabeçalho com base nos cadastros do sistema, agilizando o trabalho do técnico;
- QR Code exclusivo para cada equipamento, trazendo o histórico de cada um;
- Preenchimento por voz, ideal para o técnico fazer suas anotações com rapidez;
- Possibilidade de anexar fotos tiradas na hora, com marcação de data e horário;
- Questões com pontuação, ideal para avaliar de forma numérica a severidade das falhas;
- Assinatura digital, feita diretamente na tela do celular ou tablet do técnico;
- Personalização do relatório com cores e logo da sua empresa;
- Envio automático do relatório preenchido por e-mail ou WhatsApp;
- Possibilidade de criar seu próprio formulário com as questões que fazem sentido para o seu negócio e mais de 13 opções de resposta, como checklist, textos curtos ou longos, valores de peças e serviços, entre outros;
- E muito mais!
Todos os modelos do Produttivo são preenchidos diretamente pelo celular do técnico durante a auditoria, assim não é preciso transcrever as informações depois. Além disso, todos os dados ficam armazenados em nuvem, para que nada se perca.
Conheça alguns dos outros modelos de relatórios, checklists e ordens de serviço do Produttivo:
- Relatório fotográfico, ideal para relatórios que precisam de muitas imagens para comprovação ou para mostrar o “antes e depois”;
- Checklist de manutenção preventiva para registrar as medidas preventivas implementadas para controlar os modos de falha;
- Checklist de segurança do trabalho, desenvolvido especialmente para registrar e minimizar modos de falha que ameaçam a segurança da equipe técnica;
- Checklist de máquinas e equipamentos ideal para avaliar os ativos e manter a conformidade com a NR-12;
- Checklist de combate a incêndio, para garantir a confiabilidade do sistema.
O gestor também tem acesso a tudo isso por meio do painel web, que permite criar novos modelos de relatórios, acompanhar o andamento das tarefas, direcionar serviços para o técnico e até agendar atividades por meio do plano de manutenção.
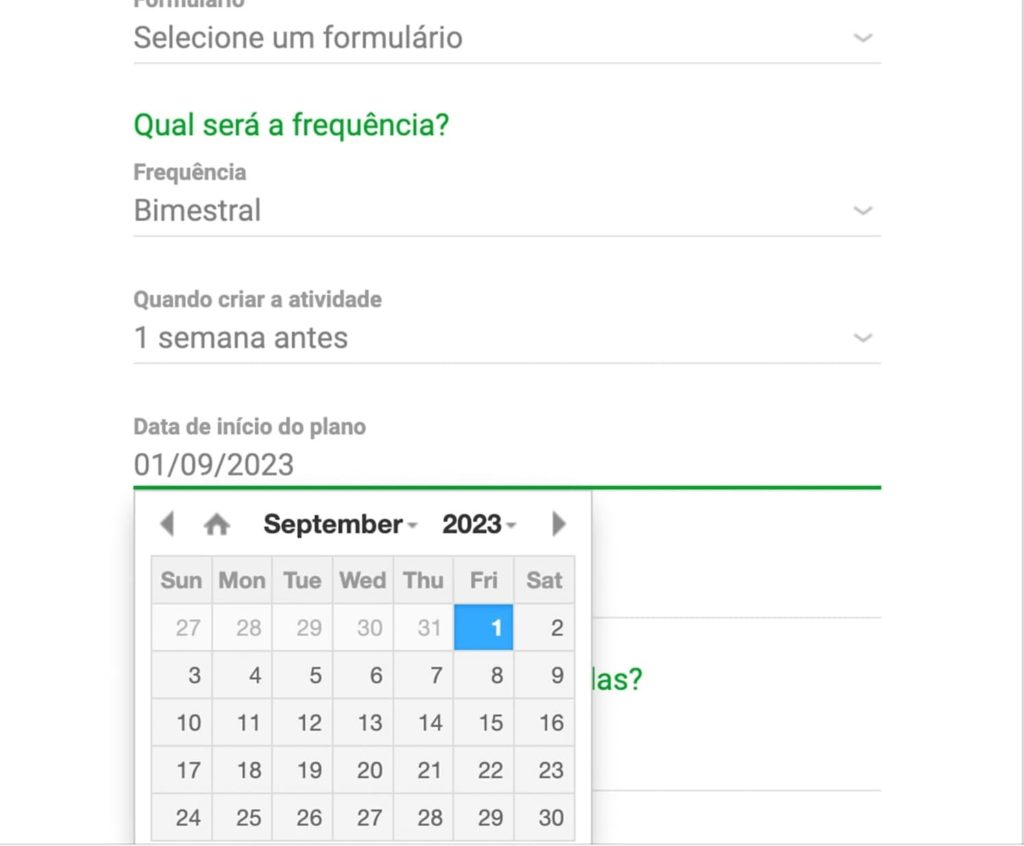
Com o Produttivo, você tem mais controle sobre a sua operação e pode registrar sua análise de modo de falha com muito mais facilidade e agilidade. Aproveite o teste grátis e comece a usar o sistema agora mesmo!