Já pensou em reduzir custos e desperdícios, aumentando a eficiência da produção usando uma única metodologia? O WMC (World Class Manufacturing) é uma ferramenta que te ajuda a alcançar esses objetivos por meio de completa mudança na cultura da empresa, baseada em pilares estratégicos.
Neste artigo te explicamos o que é o WCM, seus principais conceitos e como ele pode ser aplicado em toda operação, do setor de produção ao de manutenção.
Veja também: Software de manutenção para controle automático de serviços
WCM o que é?
O WCM (World Class Manufacturing) é uma metodologia que reúne princípios e técnicas de gestão a serem aplicadas em empresas com o objetivo de eliminar desperdícios, reduzir custos e melhorar processos.
Baseado no sistema Lean, o WCM sofreu adaptações para se encaixar nas características e necessidades do mercado ocidental, buscando estimular a melhoria contínua nas empresas, de tal forma que elas sejam consideradas empresas de “classe mundial”, ou seja, que não só consigam se destacar no mercado, como liderar o segmento em que são especialistas, entregando produtos de qualidade, com zero desperdício.
Além dos resultados obtidos com a adoção do WCM, as empresas também podem ser premiadas com certificações, sendo elas: bronze, prata, ouro e World Class. Conforme os resultados obtidos é possível chegar mais longe na certificação.
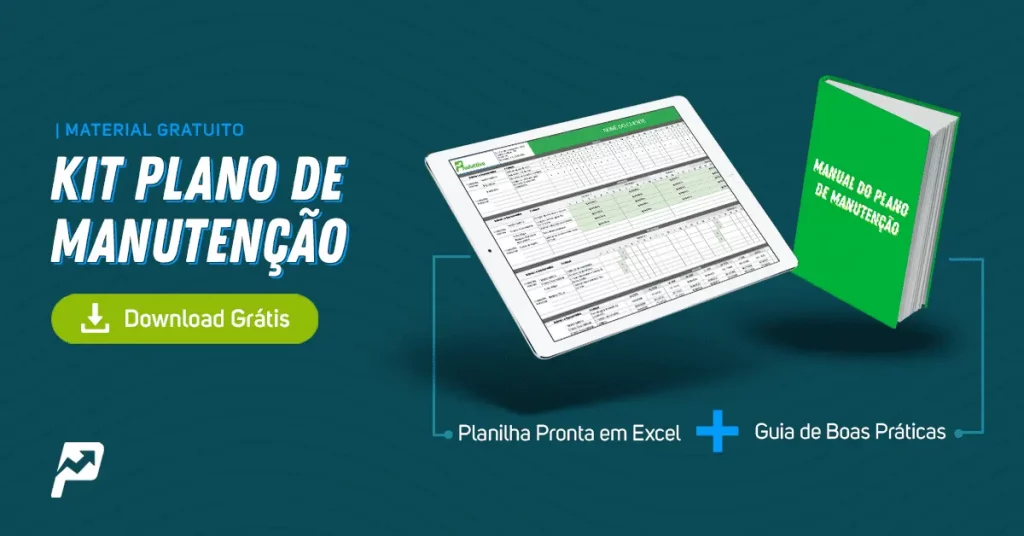
Qual a diferença entre TPM e WCM?
A manutenção produtiva total (TPM) é um conjunto de ações que têm como objetivo minimizar erros e aumentar a produtividade de equipamentos através do estabelecimento de rotinas de manutenção e do acompanhamento de performance dos ativos.
Já o WCM, como vimos, é uma metodologia que pode ser aplicada em todo o processo produtivo, independente do setor. Seu propósito é alcançar excelência operacional na produção, no controle de qualidade, na logística e nas rotinas de manutenção.
Qual a diferença entre Lean e WCM?
O WCM surgiu a partir do sistema Lean, replicando para a sua metodologia o conceito já consolidado de melhoria contínua. A diferença é que a metodologia WCM foi criada especialmente para atender as necessidades e características do mercado ocidental, que demandava resultados rápidos, utilizando a menor quantidade de recursos possíveis.
Outra diferença é que o sistema Lean se baseia apenas em princípios, e os resultados que são alcançados a partir dessa metodologia não estão atrelados a ferramentas definidas. Já o WCM possui ferramentas bem definidas para adoção da metodologia, além de mecanismos de classificação e avaliação por meio de auditorias.
Veja também: Depreciação de máquinas e equipamentos: como calcular e evitar
Benefícios da gestão WCM nas empresas
Ao implementar o WCM as empresas podem ver resultados consistentes em todos os setores, como:
- Redução nos custos de manutenção;
- Melhora de segurança para os operadores;
- Diminuição de desperdícios;
- Melhora na qualidade dos produtos;
- Redução na necessidade de manutenções corretivas;
- Resolução de problemas feitos de maneira mais rápida;
- Otimização de processos;
- Aumento de produtividade;
- Melhora no desempenho dos ativos;
- Redução de paradas não programadas;
- Aumento de satisfação dos clientes;
- Redução de lead time;
- Redução de produtos em estoque;
- Entre outros.
Otimize os resultados de manutenção através do nosso plano de manutenção para baixar gratuitamente
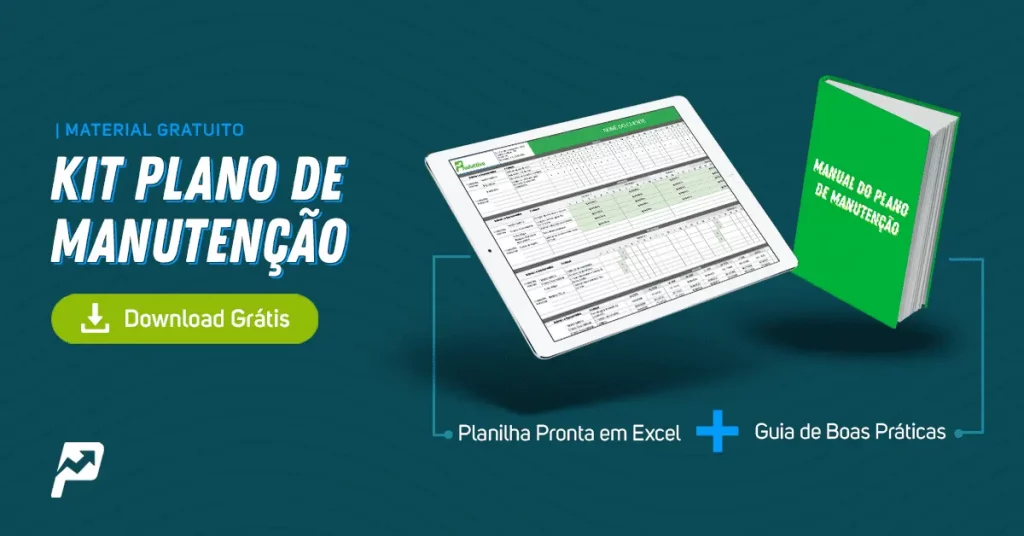
Como implementar a metodologia WCM na sua empresa?
A implementação do WCM nas organizações deve começar com uma área modelo, para só então se expandir para outros setores da empresa.
Isso acontece porque a metodologia é complexa e repleta de detalhes, além disso os gestores conseguem ter mais controle sobre sua aplicação e sobre os resultados alcançados, conseguindo empregar os aprendizados nas próximas etapas.
Separamos um passo a passo que vai te ajudar a começar a implementar as técnicas do WCM na sua empresa, confira:
- Escolha a área que servirá de modelo para a implementação do WCM. Opte pelo setor que apresenta mais problemas, resultados insatisfatórios ou os gargalos mais recorrentes, porque serão áreas que apresentarão maiores oportunidades de melhorias;
- Comece a estrutura a aplicação da metodologia através de um planejamento que leve em conta todos os princípios do WCM (mais para frente elencamos todos os princípios para você não esquecer de nenhum);
- Entenda e defina quais ações podem ser implementadas levando em conta os princípios do WCM e os objetivos da empresa (redução de falhas, perdas, desperdícios, defeitos, geração de resíduos, etc);
- Capacite os profissionais da área oferecendo treinamentos sobre WCM para que conheçam e apliquem as ferramentas necessárias;
- Garanta que profissionais altamente qualificados sejam alocados para esse setor e que eles auxiliem na implementação das técnicas de WCM;
- Use ferramentas que possam auxiliar na implementação dos princípios do WCM (mais adiante falaremos de algumas delas detalhadamente). São exemplos o FMEA, Matriz GUT, 5s 5t, Poka Yoke, Kanban e análise de causa raiz.
Usando um exemplo prático para aplicação dos passos do WCM, temos um setor de manutenção industrial cujo principal problema é resolver as constantes quebras, falhas e defeitos de um maquinário. Nesse caso o passo a passo ficaria da seguinte forma:
- O setor escolhido para começar com o WCM foi o setor de manutenção, devido às constantes quebras e falhas de maquinário, que impactam a produção e a qualidade dos produtos.
- Para resolução do problema do maquinário, as ações serão desenvolvidas com base nos pilares de manutenção autônoma, manutenção planejada e gestão preventiva dos equipamentos;
- Dentro dos princípios as ações escolhidas para serem implementadas foram:
- Manutenção autônoma: Capacitação dos profissionais e adoção de rotinas de inspeção, limpeza e lubrificação para o equipamento;
- Manutenção planejada: Análise da causa raiz das quebras do equipamento e criação de um plano de manutenção para o ativo, estabelecendo a periodicidade de realização das manutenções;
- Gestão preventiva dos equipamentos: Envolvimento da área de engenharia nos projetos dos equipamentos, integração de fornecedores no projeto, desenvolvimento e monitoramento de todas as etapas do projeto;
- Foram estabelecidos treinamentos para os operadores, manutentores e demais envolvidos no setor de manutenção que cuida do ativo;
- Profissionais altamente qualificados foram direcionados ao setor;
- As ferramentas utilizadas foram: análise de causa raiz, FMEA, ciclo PDCA e matriz GUT.
Assim que o WCM for aplicado, surgirão aprendizados que podem ser aplicados para outras áreas e as melhores práticas adotadas podem ser disseminadas por toda a empresa.
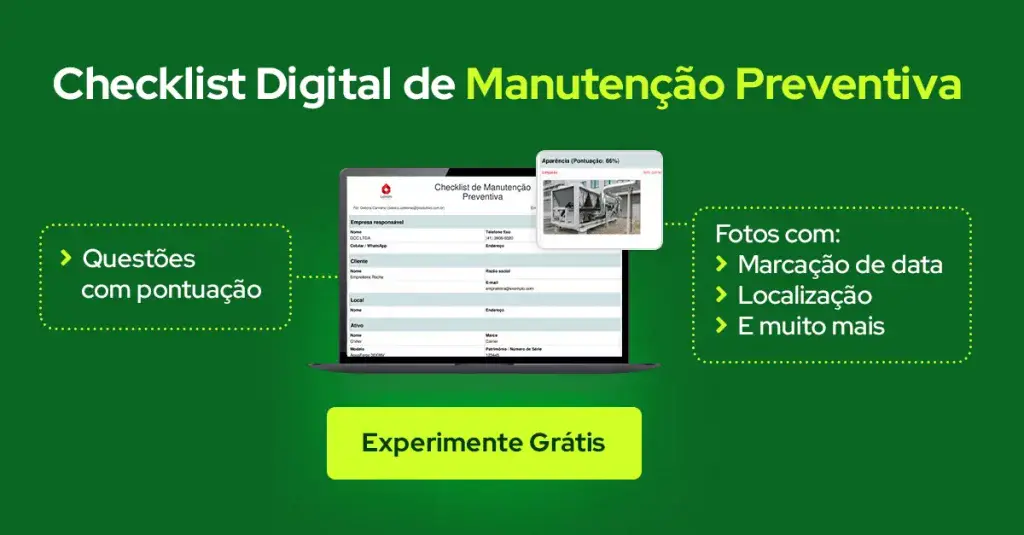
Como é o sistema de avaliação WCM?
A avaliação do WCM é realizada por uma auditoria externa que faz uma análise, duas vezes por ano, sobre os resultados obtidos em cada um dos pilares do WCM.
A nota vai de 0 a 5 e todos os pilares são avaliados individualmente considerando o nível de expansão, profundidade e maturidade dos princípios adotados.
Através das notas a empresa consegue identificar quais pilares precisam ser aprimorados, quais estão em perfeita conformidade e também consegue descobrir como está o seu nível de implementação do WCM, de acordo com a certificação que recebe, que pode ser:
- Bronze: ≥ 50 pontos;
- Prata: ≥ 60 pontos;
- Prata: ≥ 60 pontos;
- Ouro: ≥ 70 pontos;
- World Class: ≥ 85 pontos.
Quais são os pilares do WCM?
Conhecer os pilares do WCM é fundamental para a implementação da metodologia nas empresas. Eles são divididos em duas partes, com 10 pontos centrais. Entenda mais sobre cada um:
Pilares técnicos do WCM
Os pilares técnicos devem ser adotados por todas as etapas de produção e tratam sobre temáticas como manutenção, custos e qualidade. Veja detalhadamente o que cada princípio instrui:
1. Segurança
Tem como objetivo melhorar a segurança no local de trabalho, diminuindo os riscos de acidentes, reduzindo a incidência de atos inseguros. Também busca desenvolver uma cultura preventiva, assegurando a integridade e o bem-estar dos operadores.
Para a sua aplicação podem ser desenvolvidas análises de riscos, criação de mapas de riscos e realização de manutenções preditivas em equipamentos.
2. Desdobramento de custos
No desdobramento de custos do WCM a empresa deve mapear todos os custos desnecessários para que sejam reduzidos ao máximo, começando por aqueles que geram mais perdas e oferecem maior potencial de redução.
Como ações práticas é possível realizar a matriz de perdas, definir o orçamento dos próximos meses ou do próximo ano e estruturar um plano de redução de custos.
3. Melhoria contínua
A melhoria contínua defende a constante adoção de técnicas, estratégias e ferramentas para que a evolução da organização não tenha fim e sempre esteja sendo aprimorada. É através dela que há a melhora de performance e a identificação dos métodos certos para cada problema encontrado.
Para implementá-la realize treinamentos, monitore o andamento de projetos e valide resultados de outras ações e experimentos que foram feitos, pensando nas próximas aplicações.
4. Manutenção Autônoma
A manutenção autônoma se traduz na capacitação dos operadores para a realização de uma manutenção eficiente, na melhora da disponibilidade e desempenho dos equipamentos e na realização de rotinas recorrentes de limpeza, lubrificação, inspeções e demais ajustes pontuais.
Com isso, se pretende reduzir a incidência de quebras e falhas, melhorar a eficiência global (OEE) das máquinas, garantir maior qualidade nos produtos e aumentar a vida útil dos ativos.
5. Manutenção Planejada
Ao restaurar as condições de funcionamento dos equipamentos, a manutenção planejada busca aumentar a eficiência e reduzir custos de manutenção, fazendo com que o MTB aumente e o MTTR diminua.
As ações adotadas consistem na elaboração de um plano de manutenção preventiva, análise de causa raiz e realização de atividades que recuperem as condições originais dos maquinários.
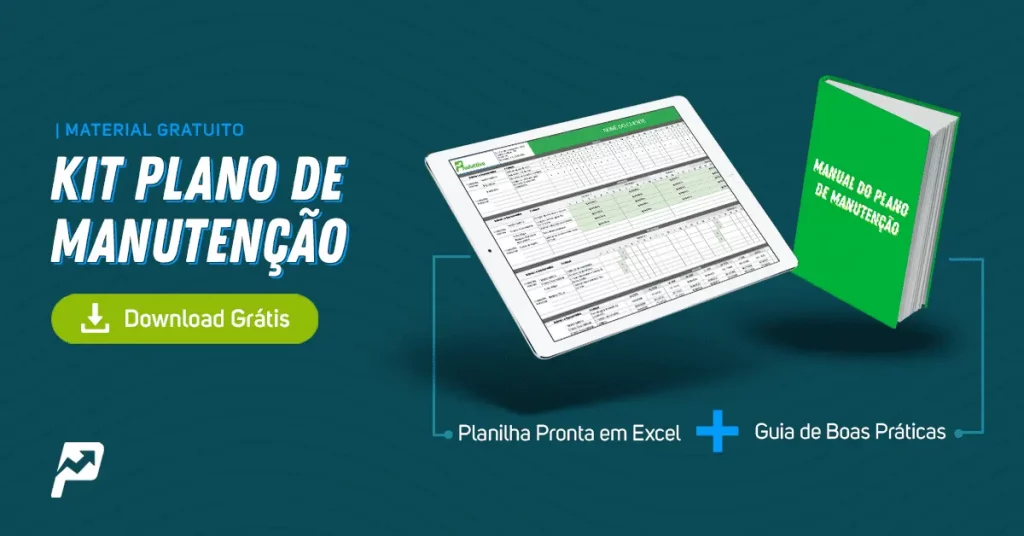
6. Controle de qualidade
O controle de qualidade deve garantir a máxima qualidade dos produtos e satisfação dos clientes com o mínimo de custo de produção. Por isso, deve alinhar variáveis envolvidas no processo, reduzir estoques e com eles reduzir também as possibilidades de danos aos produtos.
Os resultados podem ser observados na redução de defeitos, refugos e retrabalhos e no aumento do NPS e outros mecanismos de pesquisa de satisfação do cliente.
7. Logística e serviço ao cliente
Implementando uma boa gestão logística o lead time é reduzido, assim como os níveis de estoque que, por sua vez, têm um impacto direto na redução de custos. Além disso, as movimentações internas são minimizadas e os fluxos de atendimento ao cliente ficam mais enxutos.
Para aprimorar a logística, a empresa pode apostar em mapeamentos de fluxo de valor, melhorar os sistemas de programação interna e externa, os layouts e as embalagens.
8. Gestão preventiva dos equipamentos
A gestão preventiva dos equipamentos deve ter como foco o aumento da confiabilidade, a diminuição do custo de vida e a redução da necessidade de manutenção dos ativos.
As ações adotadas devem se preocupar em reduzir o lead time entre a concepção e produção, melhorar a curva de aprendizado do equipamento e, consequentemente, seu desempenho. Além de adquirir novos equipamentos que sejam referências em custo, qualidade, produtividade e facilidade de manutenção.
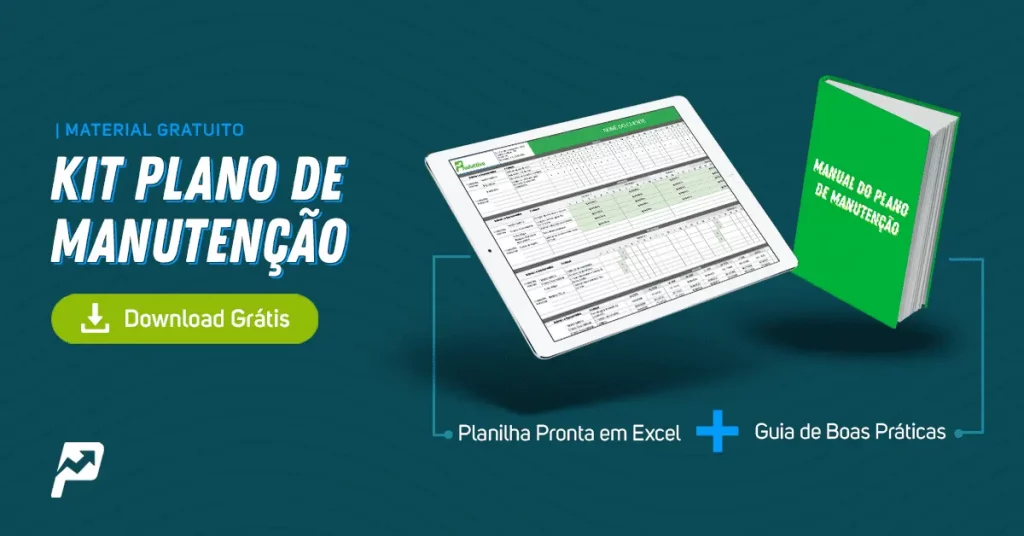
9. Desenvolvimento de pessoas
Para que o WCM tenha sucesso e adesão nas empresas, é preciso que todos os colaboradores sejam capacitados e treinados para implementar os conceitos difundidos pelo WCM, se preocupando em reduzir todos os problemas relacionados a erros humanos e atos inseguros.
Para que isso ocorra é necessário mapear conhecimentos e ações que tiveram resultados positivos durante a implementação do WMC, analisar gaps e ter um plano de treinamento para desenvolver competências essenciais dos colaboradores, bem como apresentar ferramentas que vão auxiliar na resolução de problemas.
10. Meio ambiente e energia
O último pilar técnico do WCM trata do uso correto de recursos naturais e materiais da empresa. Como foco principal está a redução do consumo de energia, o uso de energias alternativas, a promoção de conscientização ambiental e a restauração de equipamentos que têm grande consumo.
Para colocar o pilar em prática, realize auditorias internas focadas no cumprimento das exigências da norma ISO 14001, mapeie e controle o consumo de energia de cada equipamento e melhore as condições dos ativos.
Pilares gerenciais do WCM
O WCM, antes de tudo, precisa ser uma filosofia praticada pelas lideranças. Por isso, o segundo pilar desta metodologia está relacionado ao comprometimento que gestores e gerências devem demonstrar. Veja o que cada um dos pilares gerenciais orientam:
1. Comprometimento gerencial
O comprometimento geral ressalta a necessidade do envolvimento das lideranças com as ferramentas, princípios e metodologias utilizadas no WCM. Afinal, quando os líderes estão engajados é muito mais fácil engajar os colaboradores também.
Ou seja, é preciso que o WCM seja uma filosofia na empresa, direcionando todas as atitudes da liderança, mudando e remodelando a cultura da organização, das mais altas hierarquias até o chão de fábrica.
2. Clareza de objetivos
Outro ponto que impacta no engajamento e direcionamento da equipe são os objetivos. Logo, eles devem estar claros e serem muito bem construídos desde o início da aplicação do WCM, pois eles vão nortear todas as ações subsequentes.
Ao determinar os objetivos é preciso que as lideranças mostrem os parâmetros e resultados esperados e o caminho para alcançá-los.
3. Mapeamento das etapas para o WCM
Logo em seguida dos objetivos, deve vir o mapeamento, que serve como um planejamento que determina como será a implementação do WCM, quais indicadores devem ser acompanhados e os resultados esperados.
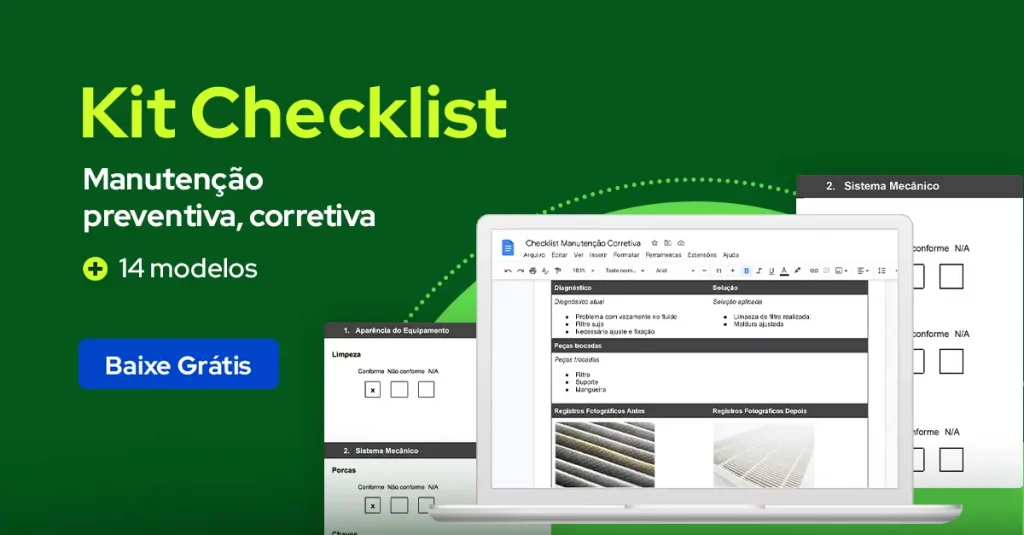
4. Alocação de pessoas qualificadas
Para acelerar a adoção do WCM a contratação e o envolvimento de pessoas altamente qualificadas, que entendam a metodologia, são mais do que necessárias.
Esses profissionais serão a base para a implementação do WCM e os responsáveis por garantir que os objetivos estão sendo seguidos.
5. Comprometimento da organização
A melhoria contínua proposta pelo WCM só acontece se os trabalhadores que movimentam a organização estiverem engajados. Por isso, a liderança precisa pensar em formas de garantir esse comprometimento.
6. Focar em melhoria contínua para obter competência organizacional
A cultura da melhoria contínua deve ser amplamente estimulada entre os colaboradores, de forma gradual e em conjunto com a capacitação dos colaboradores que devem desenvolver as competências necessárias para prevenir, resolver problemas e avaliar as soluções aplicadas.
7. Tempo e orçamento
Desenvolver o WCM nas empresas demanda tempo e investimentos, sem isso é impossível fazer a metodologia acontecer na prática. Por isso, a liderança deve estar comprometida em dedicar tempo e orçamento ao projeto, afinal, vimos que serão necessários treinamentos, qualificação de pessoas e investimento em melhorias para alcançar os resultados desejados.
8. Nível de detalhe
Esse pilar chama a atenção para o nível de detalhe que o WCM deve alcançar. É preciso definir as etapas necessárias para fazer o projeto acontecer, as metas a serem acompanhadas e o investimento necessário, tudo de forma detalhada, passo a passo.
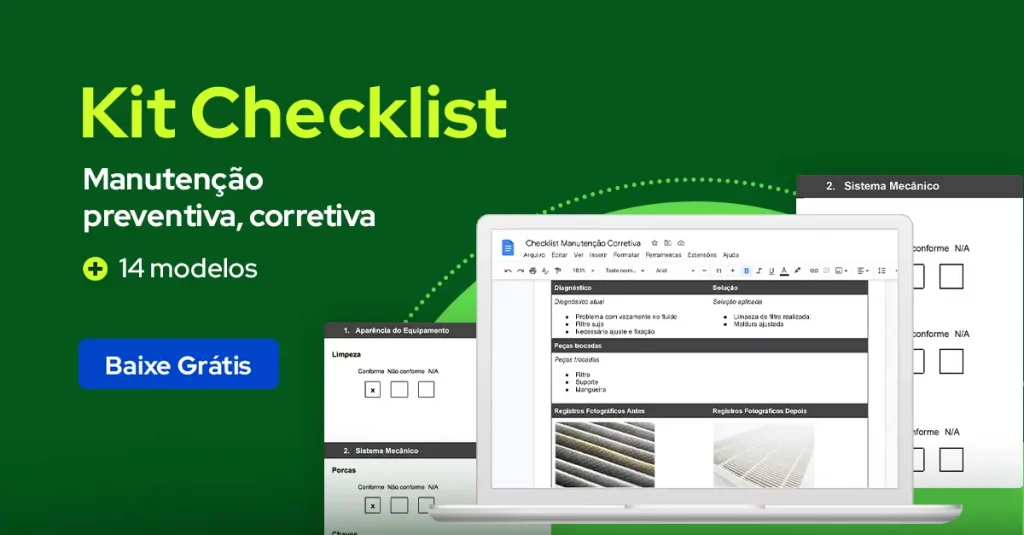
9. Nível de expansão
O nível de expansão diz respeito à expansão do projeto: qual área vai começar a implementar o WCM? Qual será a ordem de setores que vai receber o WCM? Quais são os resultados que devem ser atingidos durante a implementação do WCM?
Todos esses questionamentos devem ser respondidos pela liderança para que sejam definidos começos, finalizações e próximos passos e para que a implementação do WCM não acabe logo no início, por não ter um vislumbre de para onde ir em seguida.
10. Motivação da equipe
E, por último, a motivação da equipe deve ser sempre estimulada pela liderança, que precisa criar mecanismos para que os colaboradores se mantenham interessados e aplicando os pilares do WCM em seu dia a dia.
Quais são as 7 ferramentas WCM?
Existe uma variedade de ferramentas que podem ser utilizadas no WCM, tudo depende do objetivo de sua aplicação e do que você deseja alcançar com ela.
É comum que para cada fase da produção um tipo de ferramenta possa ser aplicada e, em alguns casos, umas são mais ideais do que outras ou podem até mesmo ser utilizadas em conjunto.
Para que você conheça as principais e mais utilizadas, separamos sete ferramentas principais:
5G
A metodologia 5G ajuda a analisar o porquê perdas, defeitos, avarias e anomalias acontecem, encontrando uma solução definitiva para o problema em questão.
Para isso, a ferramenta se utiliza de cinco definições que têm como objetivo detalhar o problema e assim evidenciar a sua causa raiz. As conclusões acontecem a partir de observações realizadas no local em que o problema aconteceu e avaliações de registros ou documentos.
Entenda o que cada definição significa e quais ações devem ser tomadas para identificar o problema:
- Gemba (Fábrica): A primeira ação deve ser ir até o local em que aconteceu o problema e realizar sua própria observação;
- Gembutsu (Material): Em seguida avalie qual é o problema, examinando-o e medindo-o;
- Genjitsu (Contexto): Analise dados e outras informações que te ajudem a entender o que mudou, confira históricos e demais registros;
- Genri (Teoria): Consulte os registros sobre os padrões de produção (desenho, especificações, ciclos de trabalho)
- Gensoku (Regras e Princípios): Verifique se os padrões foram seguidos durante a produção.
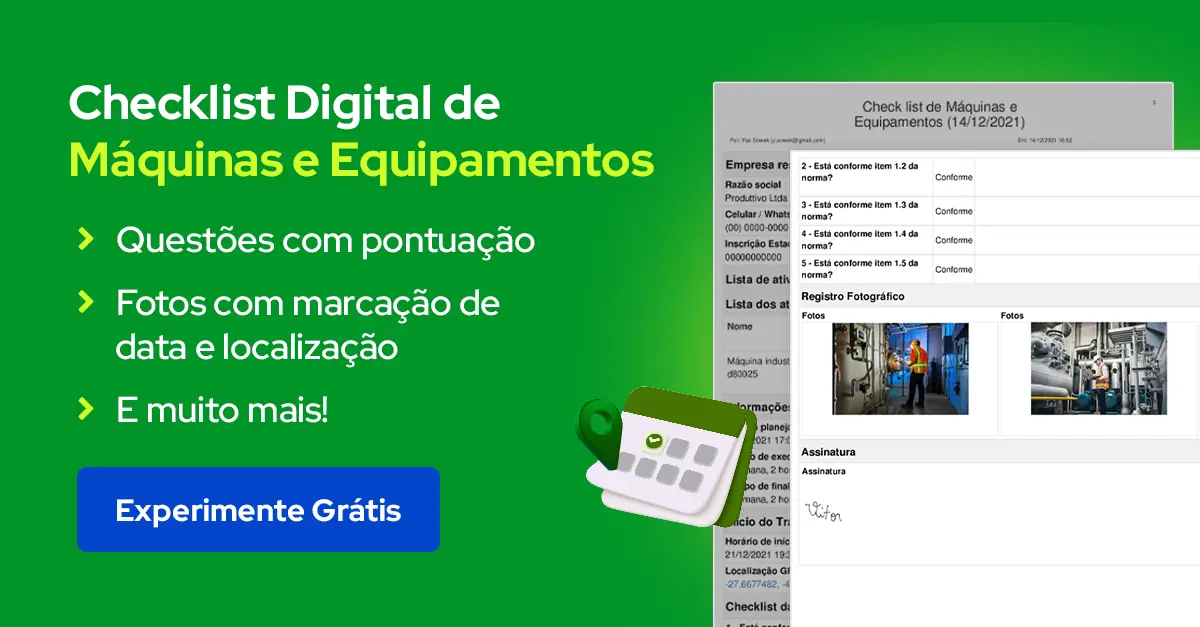
5W2H
Através de sete perguntas o 5W2H facilita a criação e aplicação dos planos de ação, porque ao detalhar o que deve ser feito, as ações ficam muito mais claras.
Veja quais são as perguntas que seu plano de ação deve responder:
- What? (O que?) – Se refere ao problema ou ao objetivo do plano de ação;
- Why? (Por quê?) – Aqui devem ser elencadas as justificativas do projeto ou as explicações do porquê aquele plano de ação foi escolhido;
- Where? (Onde?) – Pode ser tanto o local em que se encontra o problema ou o local/setor que precisa atingir um objetivo;
- When? (Quando?) – Data de início e fim do plano de ação. Aqui podem ser definidas entregas menores, em etapas, dependendo do objetivo.
- Who? (Quem?) – Descrição dos envolvidos nos projetos e quais tarefas desempenham;
- How? (Como?) – Detalhamento de como a ação será feita para alcançar o resultado almejado;
- How much? (Quanto?) – Qual o orçamento disponível para a realização das ações.
5 Porquês
O 5 porquês é outra metodologia de análise de causa raiz que serve para chegar ao motivo exato que ocasionou aquele problema, de tal forma que ao resolvê-lo o problema é definitivamente solucionado.
Essa ferramenta determina que ao se perguntar pelo menos cinco vezes “Por quê?”, a causa raiz do problema estará descoberta, isso porque a repetição da pergunta faz com que as respostas sejam cada vez mais detalhadas e assertivas.
Veja um exemplo prático de sua aplicação no WCM:
- O maquinário parou de funcionar. Por que o maquinário parou de funcionar?
- Porque depois de parar de funcionar enquanto estava sendo usado, identificamos que ao acionar o aparelho para iniciar novamente, ele não voltou a ligar. Por que não foi possível ligar o maquinário?
- Verificamos que uma peça estava quebrada. Por que a peça foi quebrada?
- A peça era muito antiga. Por que a peça era tão antiga?
- Porque o maquinário não foi inspecionado. Por que o maquinário não foi inspecionado?
- Porque não existe um plano de manutenção preventiva para os maquinários da empresa.
Kaizen
A metodologia Kaizen ajuda a empresa a colocar em prática mudanças que podem estar relacionadas a qualquer fase do processo de produção. Sua aplicação ocorre em três fases principais:
- Preparação: Como o nome sugere, a fase de preparação precede a implementação da mudança e serve para preparar os profissionais envolvidos, fornecer informações, apresentar as etapas de realização e coletar dados importantes para a próxima fase. A preparação acontece em média de 3 a 8 dias antes da mudança.
- Evento: É quando a mudança é implementada e tem duração de 5 dias. Nessa fase o profissional deve se dedicar exclusivamente ao projeto
- Follow-up: O controle e as análises sobre a etapa de mudança acontecem no follow-up, que tem como objetivo garantir que as implementações realizadas na fase anterior, continuem acontecendo e que a empresa não volte ao que estava antes de começar o projeto. O follow up leva entre 15 a 20 dias e demanda dedicação parcial da equipe.
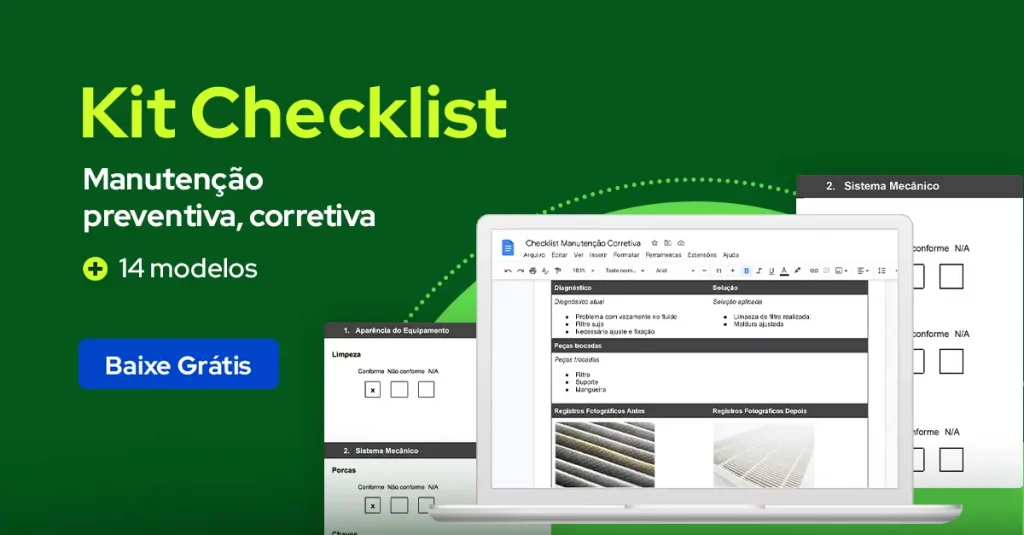
PDCA
O PDCA é muito utilizado na aplicação de planos de ação, de modo a estimular a melhoria contínua, por isso é um processo cíclico, que nunca tem fim. Para implementá-lo é necessário seguir as etapas descritas abaixo:
- Plan (Planejar): Comece planejando quais ações serão implementadas, quais problemas devem ser solucionados, qual o objetivo do plano de ação e também as hipóteses que serão verificadas;
- Do (Fazer): Coloque em prática o que foi planejado na fase anterior. Não se esqueça de acompanhar e registrar os dados provenientes da ação para a fase seguinte;
- Check (Checar): Analise os dados coletados na fase “Do” e verifique se as metas e objetivos foram alcançados;
- At (Agir): Na última fase é necessário agir com base nos resultados do plano de ação. Caso seja necessário, faça ajustes com base nos aprendizados e comece novamente o projeto ou então inicie um novo ciclo PDCA com a próxima demanda que deve ser solucionada.
Veja também: Modelo de plano de ação: o que é, para que serve e como fazer?
POP
O procedimento operacional padrão (POP) aplicado ao WCM é utilizado para estabelecer rotinas claras de produção e criar padrões de operação para, a partir disso, garantir que os erros humanos sejam reduzidos e que as ações identificadas como positivas dentro de cada área sejam mantidas.
Para implementar o POP não existe segredo, basta criar um documento contendo o passo a passo das atividades rotineiras que a área em questão deve desenvolver. É possível incrementar o documento acrescentando as seguintes informações:
- Checklists para verificação do cumprimento do passo a passo das ações mapeadas;
- Fluxograma com a representação visual dos processos de cada área;
- Glossário com a explicação dos conceitos, siglas e jargões utilizados no documento;
- Instruções de utilização do POP;
- Índice para ajudar na localização das informações;
- Descrição do que deve ser evitado de fazer em cada atividade;
- Pontos críticos que podem surgir na realização da atividade e formas de resolvê-los;
- Listagem de equipamentos e ferramentas necessárias ao desenvolvimento de cada atividade;
- Instruções de uso de equipamentos e materiais;
- Perguntas e respostas com as dúvidas mais comuns;
- Assinatura dos responsáveis pela aprovação do POP.
Veja também: Modelo de POP: o que é POP, qual a importância e as vantagens?
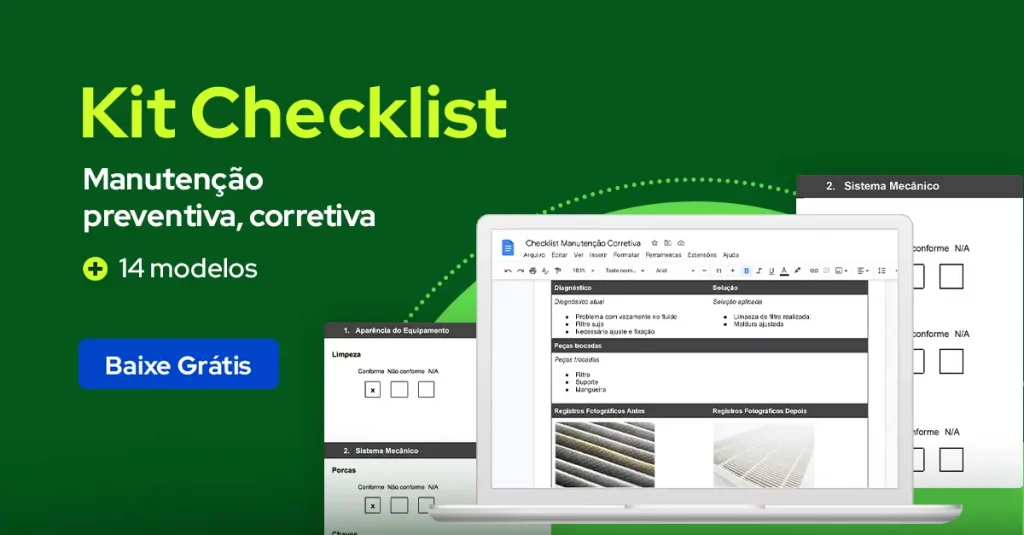
5S
O 5s combate às perdas e desperdícios nas empresas ao focar na organização e na limpeza do ambiente de trabalho, contribuindo para o aumento de produtividade da equipe.
Para implementar a ferramenta, siga os cinco conceitos abordados por ela:
- Seiri (Senso de utilização): Para implementar o senso de utilização você deve remover do ambiente de trabalho tudo que não seja mais útil para a realização das atividades (ferramentas e equipamentos quebrados, peças sem utilidade, móveis antigos);
- Seiton (Senso de ordenação): Mantenha as coisas em seu devido lugar, estipulando um espaço adequado para cada material utilizado durante as realização das atividades. Siga uma lógica na definição dos espaços, de modo a facilitar a localização dos objetos;
- Seiso (Senso de limpeza): Mantenha sempre os equipamentos, móveis e demais recursos da organização limpos e em boas condições de uso.
- Seiketsu (Senso de padronização): Crie procedimentos padrões na realização das atividades que contemplem a execução dos três sensos anteriores, para que eles estejam sempre em funcionamento.
- Shitsuke (Senso de disciplina): Desenvolva uma cultura 5s na empresa tornando a execução de todos os sensos um hábito diário entre a equipe.
Curso WCM: Quais são as certificações?
As certificações do WCM são semelhantes às do Seis Sigma, outra ferramenta de qualidade que é alinhada aos princípios do Lean Manufacturing. Porém as funções de cada nível no WCM, são diferentes. Confira quais certificações é possível alcançar de acordo com os conhecimentos do WCM:
- White Belt (WB): São profissionais que entendem os conceitos e sabem aplicar as ferramentas do WCM de maneira independente, sem precisar de orientações;
- Yellow Belt (YB): Para ser Yellow Belt o profissional precisa implementar um projeto com sucesso, seguindo um roteiro e tendo conhecimento teórico sobre ele;
- Green Belt (GB): O Green Belt realiza atividades mais complexas e tem maiores responsabilidades. É ele quem pode treinar e liderar os times de WCM;
- Black Belt (BB): Possui certificação em quatro pilares WCM e além de treinar e liderar a equipe, pode certificar outros profissionais;
- Master Black Belt (MBB): São responsáveis por gerenciar os locais de atuação dos Black Belts, têm certificação em 6 pilares do WCM e devem ter mais de dois anos de experiência na implementação do programa.
Leia também: Tudo sobre automação industrial: o que é, objetivos e vantagens
Além do WCM temos outra dica que pode te ajudar a otimizar seus resultados de manutenção: o software do Produttivo. Nele você consegue agendar manutenções periódicas, controlar o andamento das atividades e criar relatórios e checklists de manutenção de forma ilimitada.
Teste grátis por 15 dias e veja resultados por toda a operação!