Seguindo a lógica de que é melhor prevenir do que remediar, a manutenção planejada, como o próprio nome já diz, busca planejar os serviços de manutenção, estabelecendo prazos para a realização de inspeções e medidas corretivas para quando os primeiros problemas aparecem.
Neste artigo você entende quais tipos de manutenção planejada existem, os benefícios de sua aplicação e como implementá-la na sua empresa através de um passo a passo com dicas importantes.
Veja também: Modelos digitais de checklist de manutenção preventiva e de máquinas e equipamentos
O que é manutenção planejada?
A manutenção planejada (MP) é um dos pilares da Manutenção Produtiva Total (TPM) para alcançar a disponibilidade máxima dos ativos. Ela tem o objetivo de acabar com as manutenções não-programadas e, por sua vez, com as paradas inesperadas de produção ocasionadas por falhas ou quebras de equipamento.
A manutenção planejada ocorre através da criação de planos de manutenção que estabelecem quais equipamentos devem passar por inspeção, que tipos de manutenção devem ser realizadas e em qual periodicidade.
Por meio dessas ações, a manutenção planejada evita a necessidade de manutenções corretivas não-planejadas, ocasionando em economia de recursos e tempo para as empresas.
Por exemplo, se antes uma peça de um determinado equipamento era trocada só quando o defeito ocasionava a parada total de produção, ao introduzir um sistema de manutenção planejada a falha seria detectada logo no início e o melhor momento de parada do equipamento para a troca da peça seria decidido, de forma a não afetar a produção.
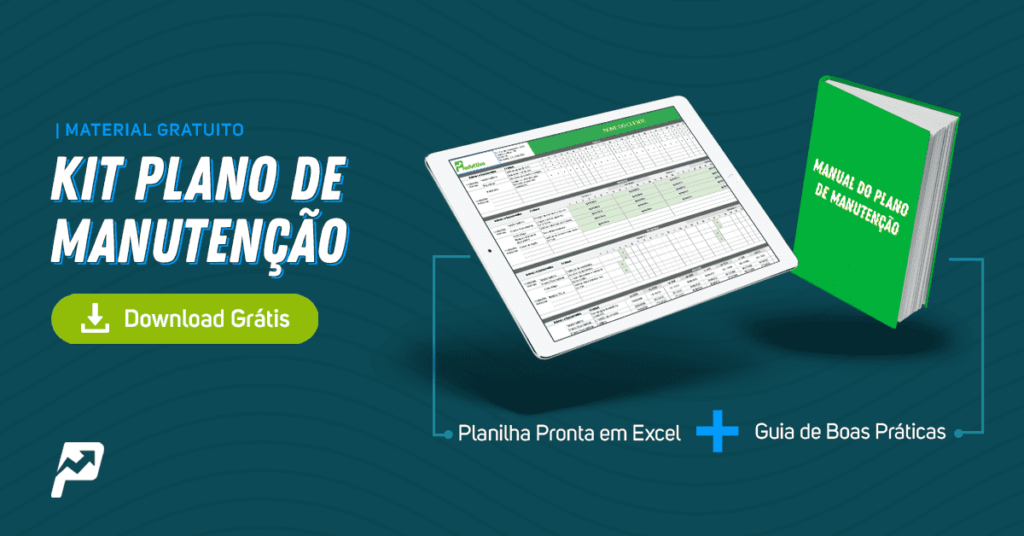
Diferença entre manutenção corretiva, planejada e não planejada
Como vimos, a manutenção planejada, ao acompanhar o funcionamento dos ativos, busca encontrar os melhores momentos para que as manutenções sejam feitas, sem ocasionar em paradas de produção não programadas pelas empresas.
Já as manutenções corretivas podem ser divididas de duas formas: as manutenções corretivas não planejadas e planejadas.
As manutenções corretivas não planejadas, como o próprio nome destaca, são realizadas em caráter emergencial, logo após algum equipamento parar. Por esse motivo, precisa acontecer o quanto antes, já que a parada não havia sido programada previamente.
A manutenção corretiva planejada é quando existe uma programação de quando os ajustes e consertos necessários serão feitos, sem interferir nas rotinas de produção das companhias.
Benefícios da manutenção planejada
A principal vantagem em realizar manutenções planejadas é garantir que o ativo não vai parar inesperadamente e, ao cumprir esse objetivo, a manutenção planejada é responsável por alcançar outros bons resultados, como:
- Diminuição da necessidade de manutenções corretivas;
- Redução dos custos de manutenção;
- Aumento de investimento de recursos e de tempo em áreas que podem aprimorar ainda mais os resultados que a empresa almeja alcançar;
- Aumento na qualidade final do processo produtivo;
- Aumento da vida útil dos equipamentos;
- Aumento da segurança aos trabalhadores;
- Redução de quebras;
- Melhora no cumprimento de prazos;
- Aumento de produtividade de ativos e da equipe;
- Otimização do gerenciamento de custos e de ativos;
- Melhoria do controle dos equipamentos.
Veja também: Contrato de manutenção preventiva: como fazer e modelo
Tipos de manutenção planejada
Dentro da manutenção planejada existem diversos outros tipos de manutenção e cada um tem um objetivo diferente. Veja quais são os principais:
Manutenção preventiva planejada
A manutenção preventiva é usada para prevenir falhas, quebras e desgastes em equipamentos através da criação de um cronograma de manutenções, que estabelece as periodicidades e os tipos de inspeção a serem realizados.
A periodicidade das manutenções preventivas podem ser baseadas no tempo ou no uso dos ativos.
Ou seja, um equipamento pode passar por vistoria depois de ser usado por tantas vezes ou depois de completar um número x de horas, parâmetro que deverá ser estipulado de acordo com o tipo de ativo. No caso de um ar condicionado, por exemplo, a recomendação é que as manutenções preventivas sejam realizadas em um intervalo de 6 a 12 meses.
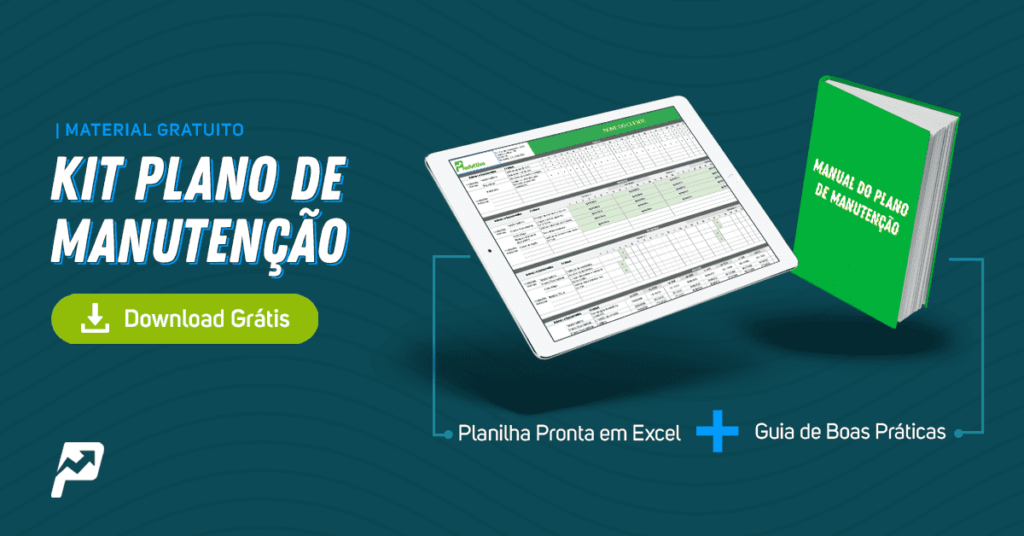
Manutenção preditiva planejada
Ao fazer uso da tecnologia, a manutenção preditiva planejada tem como objetivo monitorar o desempenho dos equipamentos de forma a antecipar falhas.
Para fazer a análise, esse tipo de manutenção planejada leva em conta uma série de indicadores relacionados a vibração, temperatura e até alterações físico-químicas de produtos utilizados nas máquinas.
Alguma ação é tomada sempre que os números indicados estão fora dos padrões estabelecidos.
São exemplos de manutenções preditivas:
- Análise de vibração: É aplicada em equipamentos rotativos e identifica os problemas através da variação dos níveis de vibração do ativo;
- Termografia: É usada em equipamentos elétricos, mecânicos, tubulações, sistemas hidráulicos e pneumáticos e monitora a variação de temperatura;
- Análise de óleo: Controla as alterações físico-químicas de óleos e lubrificantes hidráulicos;
- Ultrassom: Prevê as falhas através das vibrações e dos ruídos dos equipamentos.
Para que a manutenção preditiva seja implementada, ela deve responder a alguns critérios: os equipamentos devem permitir o monitoramento; deve ser um ativo importante devido aos altos custos das tecnologias envolvidas e todo o processo deve ser acompanhado, até mesmo os motivos que levaram as falhas.
Manutenção planejada não-programada
Falhas acontecem e mesmo que não estejam previstas é preciso saber lidar com elas, resolvendo-as da maneira mais rápida e segura possível. É com esse cenário que a manutenção planejada não-programada se preocupa.
Ou seja, depois que um equipamento apresenta falhas, qual será a ação tomada? Na manutenção planejada não-programada todas as ações corretivas já estão mapeadas e a equipe já sabe o que fazer, porque previamente identificou os possíveis acontecimentos e formas de consertar o ocorrido sem ocasionar em grandes paradas na linha de produção.
Manutenção corretiva planejada
A manutenção corretiva planejada acontece quando são percebidas alterações no desempenho de um equipamento, como quando o ativo apresenta vibrações diferentes ou pequenas falhas.
Ou seja, a manutenção corretiva planejada acontece quando o equipamento apresenta falhas, mas ainda continua funcionando, diferente da manutenção corretiva não planejada, que acontece apenas após a falha funcional do equipamento, quando a operação é parada por completo.
Assim, o objetivo da manutenção corretiva planejada é consertar essas falhas da forma mais rápida, segura e barata do que seria se uma manutenção corretiva não planejada fosse realizada.
Exemplo de manutenção corretiva planejada
Um bom exemplo que ajuda a entender o que é uma manutenção corretiva planejada, é quando a empresa já possui um estoque de peças ou maquinários de reposição. Assim, a manutenção poderá ser agendada de forma estratégica, sem atrapalhar a produção, escolhendo o melhor momento para sua realização.
Outro exemplo de manutenção corretiva planejada é quando a própria empresa decide que o equipamento vai operar até a sua quebra. Isso acontece quando a organização percebe que essa é a decisão que trará o melhor custo-benefício para a operação. Como a manutenção em modems de internet, que só é realizada depois que o aparelho apresenta defeitos.
Manutenção corretiva não planejada
Como vimos, uma manutenção corretiva pode ser tanto planejada, como não planejada.
A manutenção corretiva não planejada acontece em caráter emergencial após a interrupção do processo produtivo, ocasionada pela falha ou quebra de determinado ativo.
Esse é um tipo de manutenção que deve ser evitada, porque pode trazer sérios prejuízos às organizações como perdas de produção e de qualidade dos produtos.
Exemplo de manutenção corretiva não planejada
São exemplos de manutenção corretiva não planejada reparos de emergência; reconstrução ou salvamento de equipamentos, consertos de falhas de serviço e substituição de componentes de redutores.
Desvantagens da manutenção corretiva não planejada
A manutenção corretiva não planejada traz uma série de prejuízos, entre eles:
- Interrupção do processo de produção;
- Atraso de entregas;
- Problemas contratuais de entrega;
- Aumento de custos;
- Baixa de produtividade;
- Acidentes de trabalho;
- Perdas de produção e de qualidade de produtos.
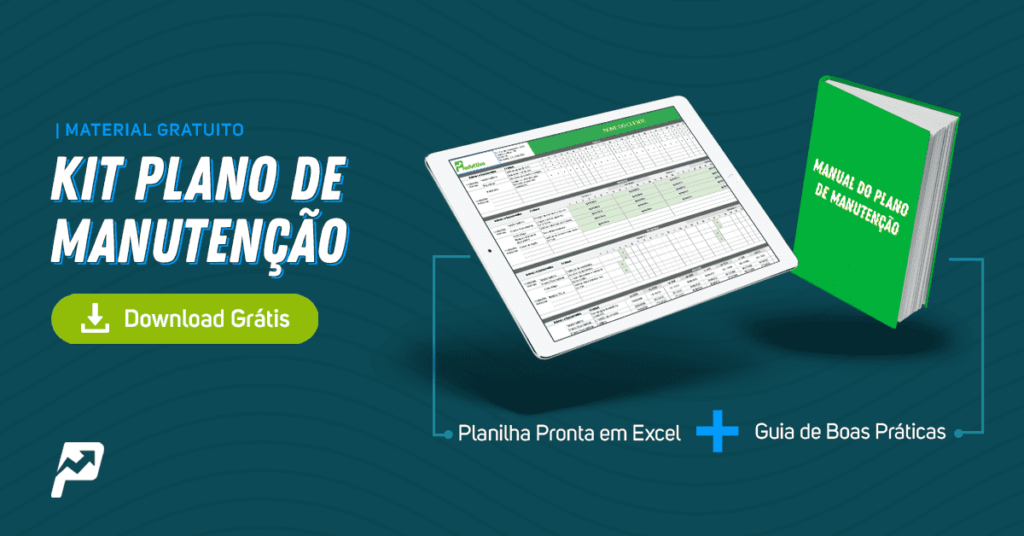
TPM Manutenção planejada
TPM é a sigla para Manutenção Produtiva Total, ela não é só um tipo de manutenção planejada, como tem a manutenção planejada como um dos seus pilares.
Assim como outros tipos de manutenção, o objetivo da TPM também é reduzir paradas de equipamentos e eliminar perdas. Ela busca alcançar esse objetivo através do alto desempenho dos equipamentos, fazendo com que eles produzam o seu máximo, com menos prejuízos.
Para isso ela se baseia nos seguintes conceitos:
- Manutenção autônoma: propõe a introdução de melhorias pela própria equipe técnica que é responsável pelos equipamentos, através de capacitação e treinamentos do time;
- Manutenção planejada: caracterizada pelo acompanhamento do desempenho dos equipamentos e instituição de um cronograma de manutenções;
- Melhorias específicas: identificação e superação da maior perda de um equipamento;
- Educação e treinamento: os colaboradores precisam saber sobre todos os processos e como usar as tecnologias a seu favor, através de um plano de treinamento;
- Manutenção da qualidade: tem como meta garantir a qualidade na manutenção, alcançando zero defeitos;
- Controle inicial: levantamento de informações importantes à manutenção;
- TPM Administrativos: eliminação de erros no setor administrativo através da metodologia de análise e solução de problemas;
- TPM Segurança, Higiene e Meio Ambiente: tem como objetivo garantir a segurança, eliminar riscos de acidentes de trabalho e promover escolhas ecologicamente corretas.
Manutenção Detectiva
A manutenção detectiva acontece através da realização de testes, mediante o uso de tecnologias que permitem identificar falhas e erros que não foram percebidos previamente nos processos rotineiros de manutenção preventiva.
Esse tipo de manutenção planejada é mais voltada para sistemas de controle, comando e proteção e é usada quando o processo é crítico e não pode ocorrer em falhas.
Um exemplo são os circuitos que comandam o gerador de um hospital. Caso haja falha neles, todos os equipamentos serão afetados e isso poderá trazer sérios riscos aos pacientes. Nesse cenário, a manutenção detectiva será responsável por testar os circuitos, de tempos em tempos, para confirmar que ele está funcionando de forma correta e que não representa riscos.
A grande diferença da manutenção detectiva, é que ela consegue identificar pequenos erros e falhas que no longo prazo podem trazer grandes impactos, se não identificados com antecedência.
Manutenção Prescritiva
Assim como a manutenção preditiva, a manutenção prescritiva faz uso da tecnologia para realizar análises e medições que mostrem o desempenho do equipamento. Dispositivos IoT e inteligência artificial são alguns dos recursos usados por esse tipo de manutenção planejada para chegar aos dados que precisa.
Mas, ao contrário da preditiva, a prescritiva se preocupa em oferecer as soluções para o equipamento, mesmo que nenhuma falha tenha sido identificada, trazendo recomendações que ajudam a otimizar o funcionamento, melhorar os resultados dos equipamentos e reduzir riscos.
Como planejar uma manutenção?
Para fazer uma manutenção planejada você precisará seguir esses 6 passos:
Veja também: Relatório de manutenção: como elaborar um de forma eficiente
1º Avalie os equipamentos
Comece fazendo uma avaliação geral dos equipamentos da organização. Tente coletar os seguintes dados:
- Como anda a performance desses ativos?
- Qual foi a última vez que uma manutenção foi realizada no equipamento?
- Quais são os custos envolvidos com a manutenção dos ativos?
- Quais parâmetros devem ser considerados para as próximas manutenções? (temperatura, vibração, etc)
- Quais são os tipos de falhas mais comuns? Elas acontecem com qual frequência e qual o impacto que geram à organização?
- Qual a causa raiz da quebra dos equipamentos?
- Quais são as metas e objetivos da manutenção?
- Quais são os números de pequenas paradas, de acidentes de trabalho e do MTBF?
Reúna todas essas informações em um relatório, criando uma espécie de inventário de ativos, com todas as informações importantes sobre ele.
Depois de ter todos esses dados em mãos é hora de analisá-los, identificando quais ativos devem ser priorizados, seja pelo desempenho que têm apresentado, pelo alto valor ou pelo nível de criticidade.
Em seguida, comece identificando qual o melhor momento para realizar a manutenção, entendendo como as paradas podem ser estratégicas, sem prejudicar o processo produtivo. E também qual o tipo de manutenção mais indicada para cada ativo, é uma manutenção preditiva ou prescritiva?
A partir disso será possível fortalecer a equipe de manutenção melhorando seus resultados, identificar onde os recursos estão sendo desperdiçados e investir mais tempo em estratégias de melhoria contínua e não apenas na resolução de falhas recorrentes.
Não se esqueça de sempre manter os dados atualizados.
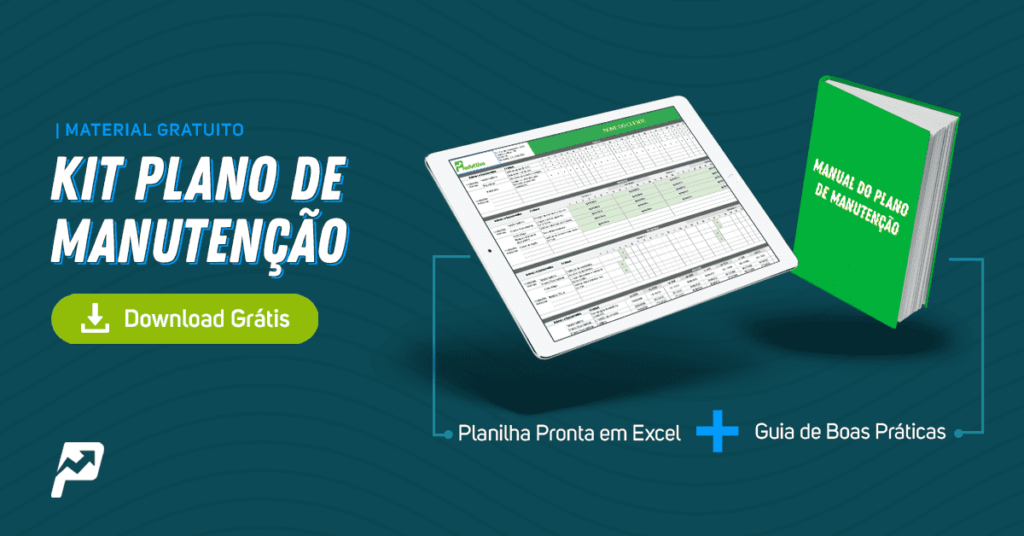
2º Corrija as falhas
No processo anterior você deve ter identificado as principais falhas. Nessa etapa o objetivo é corrigi-las.
O ideal é que você identifique a causa das falhas através de uma análise de causa raiz, reconhecendo a fonte do problema e evitando que ele volte a acontecer.
Por isso, estabeleça medidas de prevenção às falhas e aplique melhorias que as minimizem e contribuam para o aumento da disponibilidade e vida útil dos ativos.
São exemplos de medidas preventivas a troca do local de instalação do equipamento, para que ofereça melhores condições para o seu funcionamento ou a modificação dos seus parâmetros de operação.
3º Use um sistema de gestão de manutenção
Fazer o controle de manutenção e desempenho de ativos em papel não é uma boa opção. Os dados não podem ser filtrados e nem analisados. Por esse motivo, você precisará investir em um sistema de gestão de manutenção digital, que centralize as informações, ajude no controle e no acompanhamento de indicadores.
Os softwares servirão para:
- Montar um inventário de equipamentos;
- Criar e agendar cronogramas de manutenção;
- Programar atividades e manutenções;
- Administrar uso de peças e materiais;
- Gerenciar os custos de manutenção;
- Montar checklists de manutenção preventiva, ordens de serviço e demais relatórios.
- Criar um banco de dados e monitorar indicadores como volume de trabalho e principais não conformidades;
É importante que o sistema seja constantemente atualizado com informações técnicas sobre o equipamento, local de instalação, tipo de manutenção desenvolvida, periodicidade de realização, responsáveis, tempo médio e materiais necessários.
Ao implementar um sistema de gestão de manutenção planejada, os processos serão automatizados e digitalizados, facilitando a filtragem e a análise de dados, otimizando o tempo que seria gasto com controles em papel e eliminando os riscos de esquecimento de manutenções já previstas no calendário, oferecendo à empresa o pleno controle do processo de manutenção.

Veja também: Sistema de manutenção: o que é, para que serve e qual o melhor?
4º Crie planos de manutenção
O próximo passo é a criação de um plano de manutenção, que deve levar em conta as recomendações do fabricante e a realidade de operação da indústria, através das informações que já foram coletadas nos tópicos anteriores:
- Inventário dos equipamentos com avaliação de desempenho de cada um;
- Tipos de manutenções mais indicadas à cada equipamento;
- Orçamento da manutenção levando em conta os materiais utilizados e a mão de obra;
Ao ter essas informações mapeadas, um calendário de rotinas de manutenção deverá ser criado, levando em conta o nível de criticidade de cada ativo, os momentos mais estratégicos para a parada do equipamento, os responsáveis pela manutenção e os recursos necessários.
Os softwares de gestão da manutenção costumam auxiliar muito nesse processo, porque facilitam a programação das atividades e a padronização dos checklists de manutenção planejada que serão respondidos pela equipe técnica.
Lembre-se que é importante que o plano de manutenção seja constantemente revisado e atualizado, para que não existam furos ou informações erradas cadastradas nele.
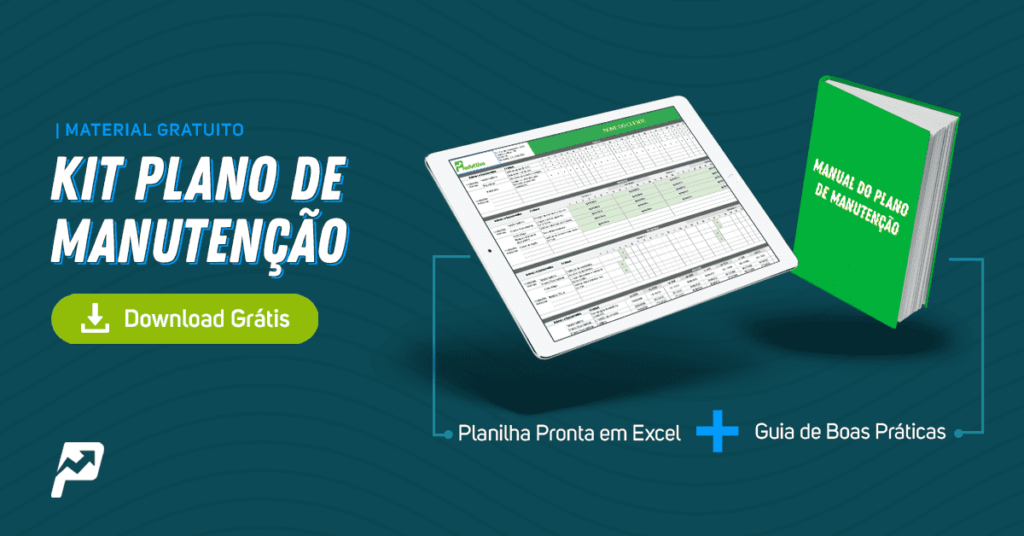
5º Invista em um sistema de manutenção preditiva
Como vimos anteriormente, a manutenção preditiva ajuda na identificação de falhas de um ativo, na medida em que monitora sinais importantes do equipamento como vibração, temperatura, ruídos e alterações físico-químicas. Por isso, vale a pena implementá-la nos ativos que permitem o seu uso e que são mais críticos.
Para sua execução é fundamental que haja um planejamento que prepare a equipe técnica para identificar quais equipamentos são os mais recomendados para utilizarem esse tipo de técnica de manutenção planejada e o investimento necessário para adquirir os aparelhos necessários e também para a capacitação dos técnicos que devem saber analisar e interpretar os dados coletados.
No planejamento é necessário incluir também planos de ação para caso alguma métrica esteja fora dos parâmetros estabelecidos, que pode ser, por exemplo, o desligamento imediato em casos de grandes alterações nos níveis vibracionais do ativo.
6º Avalie o desempenhos dos equipamentos através de indicadores
O último passo é a mensuração dos dados obtidos após a introdução do plano de manutenção planejada. Para isso, comece estipulando quais dados serão acompanhados. É importante que a coleta seja feita antes e depois das mudanças estabelecidas, para que existam critérios de comparação.
Você pode acompanhar os seguintes indicadores:
- Número de falhas pequenas;
- Número de paradas;
- MTBF e MTTR;
- Frequência de falhas;
- Taxa de manutenção periódica;
- Taxa de manutenção preditiva;
- Custos de manutenção sobre faturamento;
- Custos de manutenção sobre valor de reposição;
- Custos de manutenção sobre unidade produzida;
- Backlog;
- Disponibilidade inerente;
- Confiabilidade;
- Homem hora empregado por tipo de manutenção;
- Fator de produtividade de mão de obra.
Veja como calcular os indicadores de manutenção
Ao fazer a comparação dos dados será possível identificar se as mudanças trouxeram melhoria de resultados e como elas podem ser aprimoradas.
Lembre-se que esse deve ser um acompanhamento constante, seguido da implementação de planos de ação que visem trazer a melhoria contínua para o processo de manutenção planejada.
Estratégias de manutenção planejada
Para otimizar os resultados da implementação de uma manutenção planejada, existem algumas estratégias que podem ser aplicadas:
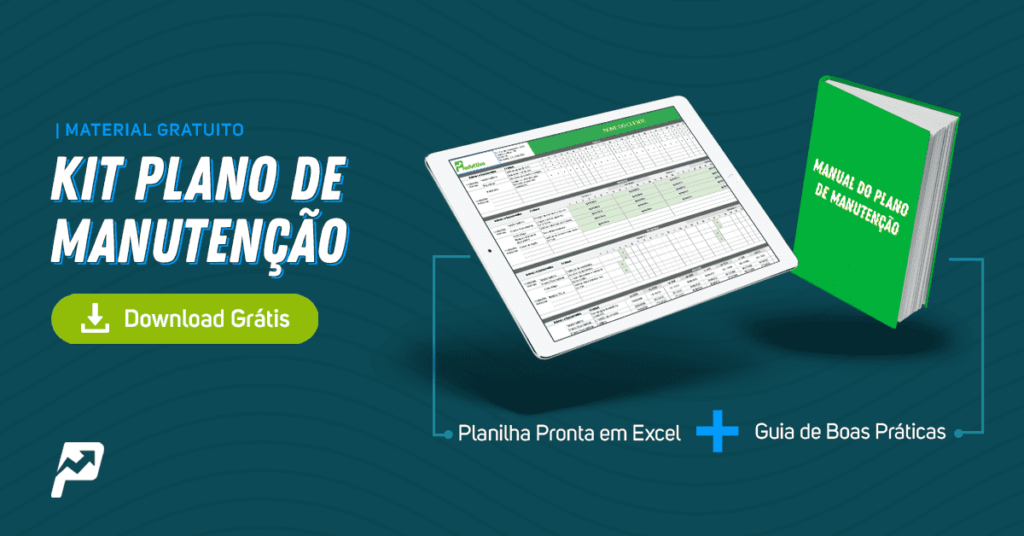
Histórico de dados e informações
A primeira estratégia de manutenção planejada que você pode aplicar é a adoção de um sistema de gestão da manutenção que permita que você tenha um histórico das informações dos ativos e que transforme os dados coletados em gráficos e disposições visuais que te ajudem a entender o que os dados dizem e a ter decisões mais assertivas, baseadas nesses números.
Afinal, ao entender o comportamento do equipamento, as atividades que foram realizadas nele e quais falhas ele apresenta, é possível identificar erros e eliminá-los de vez.
IoT na manutenção planejada
Outra estratégia é o uso da IoT (Internet das Coisas) utilizada para monitorar e administrar o funcionamento dos ativos remotamente por meio de sensores que são conectados via apps que recebem e enviam dados sobre a situação dos ativos, como temperatura, umidade, consumo de energia, entrada e saída do ar, etc.
Ao ter acesso a essas informações em tempo real os processos de manutenção planejada se tornam mais ágeis e eficientes.
Realidade aumentada
E, por último, temos a realidade aumentada que ajuda na criação de estratégias de manutenções planejadas ao possibilitar o uso de informações visuais e digitais na vida real.
Um exemplo de realidade aumentada aplicada à manutenção são os óculos de realidade aumentada, que podem ser usados em casos em que o técnico tem dificuldades para o conserto de determinado equipamento e a imagem que ele vê pode ser transmitida a algum consultor que mesmo à distância pode oferecer instruções e recomendações para a resolução do problema.
A realidade aumentada também pode ajudar na garantia de segurança do trabalho, na medida em que gestores podem acompanhar remotamente se as principais recomendações de segurança e usos de EPI estão sendo cumpridos pelos colaboradores.
O uso da realidade aumentada na manutenção também pode ser utilizado na capacitação e no treinamento da equipe, que tem acesso a simulações de como os processos acontecem, através de óculos de realidade aumentada, tablets ou smartphones, que ajudam, por exemplo, no entendimento do manuseio correto de uma peça.
Veja também: Manutenção Preventiva: como vender seus serviços e gerar mais contratos
Software de planejamento de manutenção
O uso de softwares de planejamento de manutenção digitaliza e automatiza todos os processos relacionados à programação e execução das manutenções. Trazendo resultados como:
- Melhora na organização da equipe externa;
- Eliminação de erros e retrabalhos comuns em controles feitos por papel;
- Economia de tempo e dinheiro;
- Melhora da confiabilidade;
- Padronização de processos.

Um exemplo desse tipo de sistema é o Produttivo, um app em que é possível agendar as manutenções, cadastrar ativos, locais, peças e materiais e padronizar ordens de serviço, checklists de manutenção e demais relatórios utilizados para a inspeção de equipamentos.
Em seu tablet ou celular, o técnico tem acesso a todas as informações necessárias para a realização da visita técnica: onde e quando será realizada a atividade, que tipo de relatório ele deve preencher e quais são as informações de cada ativo, através da leitura do QR Code de cada equipamento.
Já o gestor consegue acompanhar à distância o preenchimento dos relatórios através do painel web e realizar o acompanhamento do histórico de serviços e de indicadores como principais não conformidades encontradas, nível de satisfação dos clientes, volume de trabalho, tempo de atendimento, etc.
Os relatórios são todos personalizados e possuem recursos que facilitam a comprovação do trabalho realizado e aumentam a confiabilidade da empresa. É possível bloquear a galeria para introdução de fotos tiradas na hora, realizar preenchimentos por comando de voz e ainda marcar questões obrigatórias para que o técnico não se esqueça de responder.
Veja abaixo um checklist de máquinas e equipamentos gerado no Produttivo:
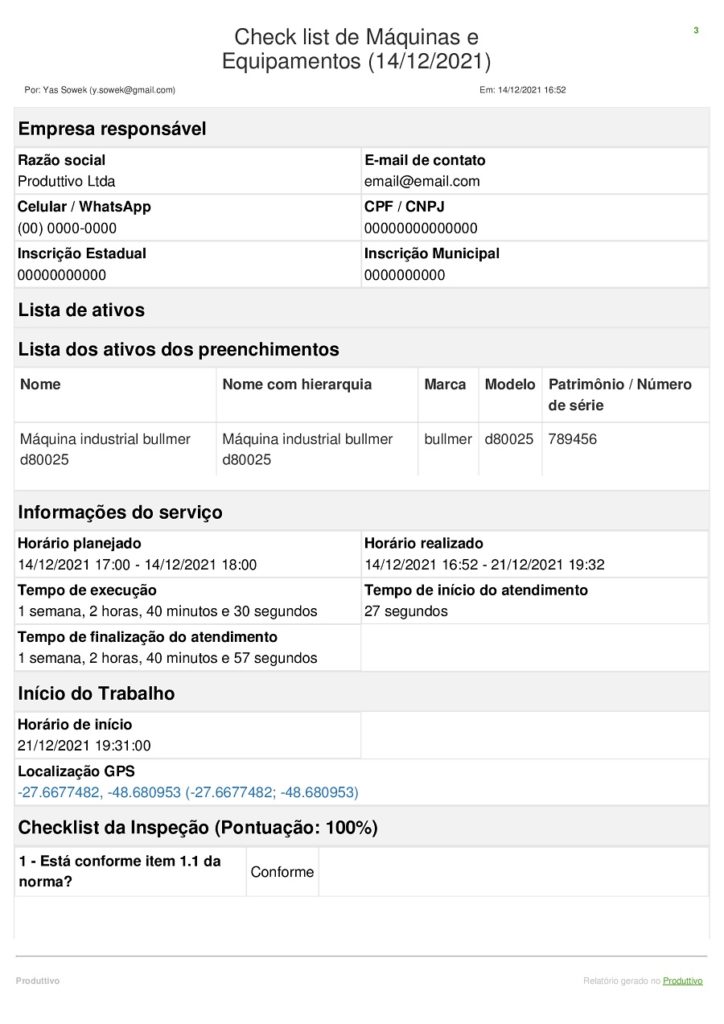
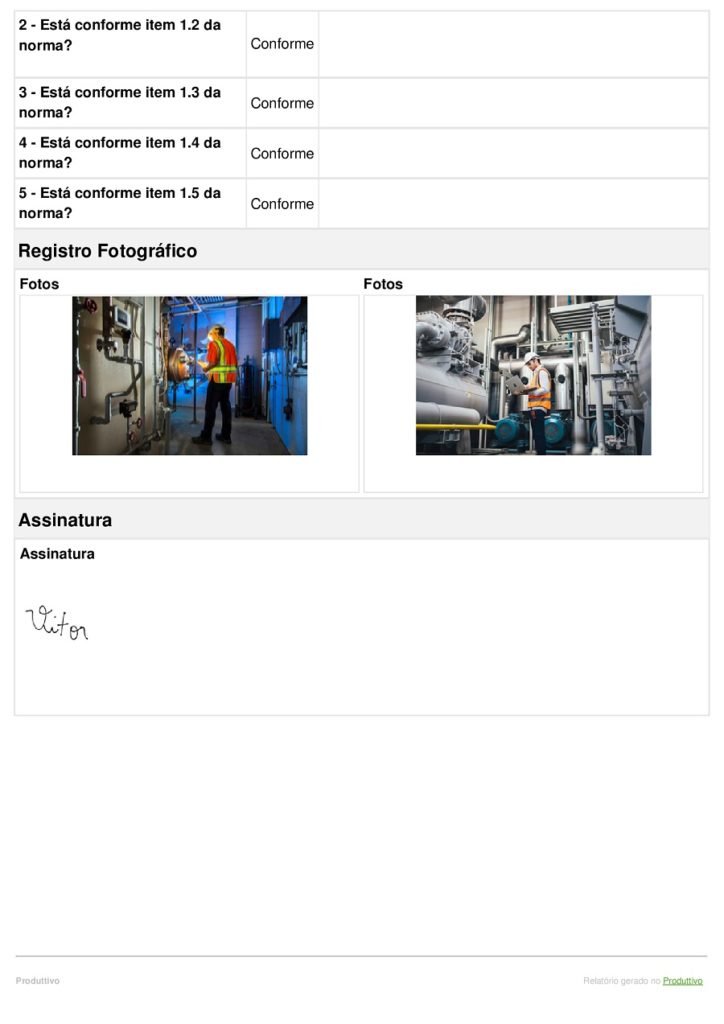
Veja também: Manutenção 4.0: o que é, como funciona e quais os objetivos
Conheça todas as funcionalidades do Produttivo e descubra como o app pode te ajudar com a realização de manutenções planejadas. Teste grátis sem precisar cadastrar o cartão de crédito!