A termografia é uma das técnicas utilizadas pela manutenção preditiva para realizar o monitoramento de equipamentos com funcionamento crítico. Ela ajuda a determinar padrões de comportamento, prever falhas e ainda facilita as tomadas de decisão.
Entenda como realizar uma inspeção termográfica, em quais setores ela pode ser aplicada e ainda tenha acesso a um modelo de relatório de termografia para usar dentro do sistema do Produttivo e melhorar a gestão dos seus ativos.
Experimente grátis: Modelo digital de checklist de manutenção preditiva para editar do seu jeito!
- O que é termografia?
- Para que serve a termografia?
- Onde a termografia é usada?
- Quando realizar uma análise termográfica?
- Como a inspeção termográfica é feita?
- Aplicações da termografia
- Quais são os equipamentos usados na análise termográfica?
- Quais são os benefícios da inspeção termográfica?
- Como implementar a termografia na gestão da manutenção?
- Exemplo de relatório termografia
O que é termografia?
A termografia é uma forma de inspeção que compõe a manutenção preditiva e serve para avaliar as condições e o estado dos ativos, com base na temperatura que eles apresentam.
Para isso, a termografia faz uso de uma câmera que capta a radiação emitida pelos maquinários, converte-a em temperatura e a exibe em uma imagem que demonstra a distribuição da temperatura daquele ativo. Os termogramas podem alcançar faixas de temperatura que vão de -40ºC a 1500ºC.
Sabendo a temperatura dos ativos, é possível identificar inúmeros problemas e falhas em fase inicial, de modo que não gerem riscos, muito menos prejuízos. São exemplos de problemas que podem ser detectados com uma inspeção termográfica:
- Corrosão;
- Entupimentos;
- Mau contato em fiações;
- Sobrecarga de circuitos;
- Oxidação dos elementos da máquina;
- Desgaste de componentes;
- Desgastes de rolamentos;
- Desalinhamento de eixos.
Muito utilizada para o monitoramento de equipamentos críticos e sistemas elétricos, a termografia é uma técnica não invasiva e que pode ser realizada por meio de sensores IoT, que além dos dados da temperatura, podem captar informações como vibração, quantidade de horas trabalhadas por ativo e identificar falhas na lubrificação, refrigeração, níveis baixos de óleo e pressão elevada.
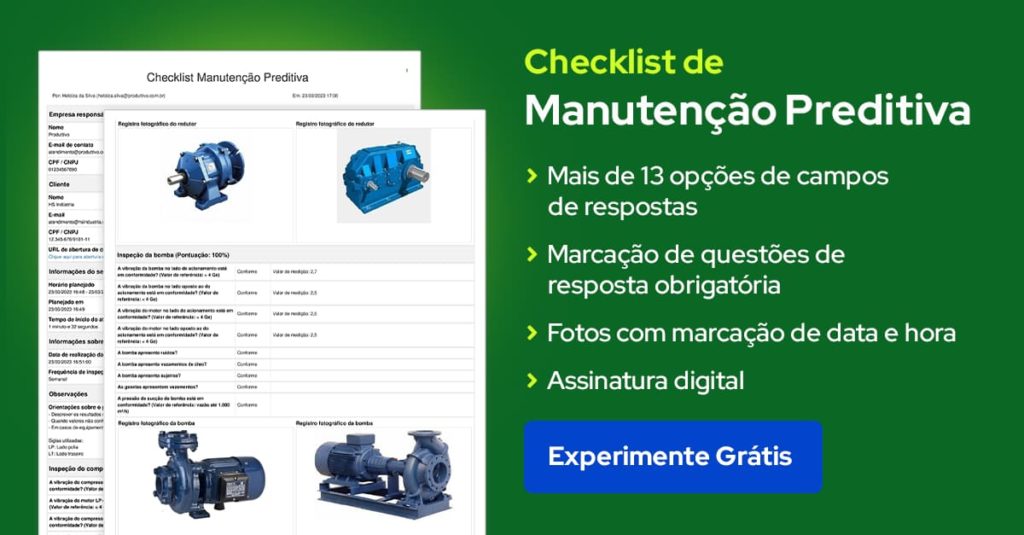
O que é termografia infravermelha?
A termografia infravermelha nada mais é do que a inspeção termográfica sobre a qual falamos logo acima. Ela também pode ser chamada com esse nome, pois utiliza um sistema infravermelho para realizar a captação das frequências eletromagnéticas emitidas pelos equipamentos, forma pela qual consegue fazer a leitura da temperatura.
Esse processo acontece por meio de uma câmera que capta essas emissões e as transforma em termogramas, ou seja, imagens que identificam e evidenciam a distribuição do calor do ativo.
Para que serve a termografia?
A termografia é utilizada para medir a temperatura de máquinas e equipamentos, estabelecendo padrões e identificando quando algum ativo apresenta temperaturas muito altas, o que pode interferir em seu funcionamento.
Além disso, a termografia também é utilizada para:
- Prolongar a eficiência operacional de sistemas elétricos;
- Tornar a gestão de ativos mais estratégica;
- Identificar anormalidades térmicas;
- Evidenciar desgastes em fases iniciais;
- Aumentar a confiabilidade dos ativos;
- Aumentar a segurança das instalações;
- Evitar acidentes com risco de incêndio.
Leia também: O que é laudo de aterramento e como fazer?
Onde a termografia é usada?
A termografia pode ser usada para diversos fins, através dela é possível monitorar, detectar e realizar diagnósticos de:
- Motores;
- Geradores;
- Transformadores;
- Conectores;
- Disjuntores;
- Fusíveis;
- Chaves seccionadas;
- Linhas de transmissão;
- Rolamentos;
- Mancais;
- Equipamentos e sistemas elétricos;
- Inspeções prediais de umidade, telhado e perda de energia;
- Imagens químicas;
- Níveis de gás e líquidos;
- Vazamentos e falhas dentro de ferramentas, tanques e paredes;
- Prevenção contra incêndios, panes elétricas e sobrecargas de sistema.
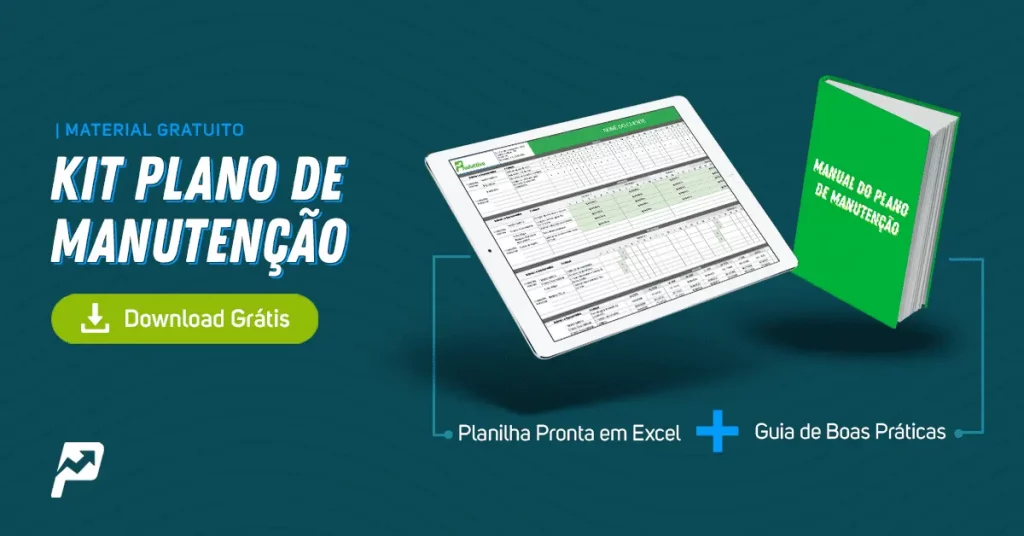
Quando realizar uma análise termográfica?
A análise termográfica deve ser realizada pelo menos uma vez ao ano de acordo com o que está estabelecido no plano de manutenção dos equipamentos.
O plano de manutenção deve ser construído levando em conta o histórico de funcionamento do ativo, as recomendações do fabricante, as análises realizadas durante manutenções preventivas, o histórico de não conformidades já apresentadas pelo equipamento, o tipo de ativo, o nível de criticidade e a vida útil do sistema elétrico.
Além disso, inspeções devem ser realizadas caso algum desses sinais seja detectado:
- Alterações de temperatura de equipamentos elétricos e mecânicos que estejam em desconformidade com os parâmetros apresentados;
- Interferências na iluminação quando equipamentos são acionados;
- Mudanças de layout para a instalação de novos equipamentos;
- Variações de energia elétrica;
- Aumento no consumo de energia elétrica;
- Queda de rendimento em ritmos normais de operação;
- Vibração acentuada;
- Odores de isolamento ou encapsulamento queimados de fios e cabos.
Para que você garanta a eficiência operacional dos ativos com um plano de manutenção bem construído, o Produttivo preparou um material gratuito que vai te ajudar a criar suas rotinas de manutenção, sem esquecer de nenhuma inspeção, basta clicar no banner abaixo:
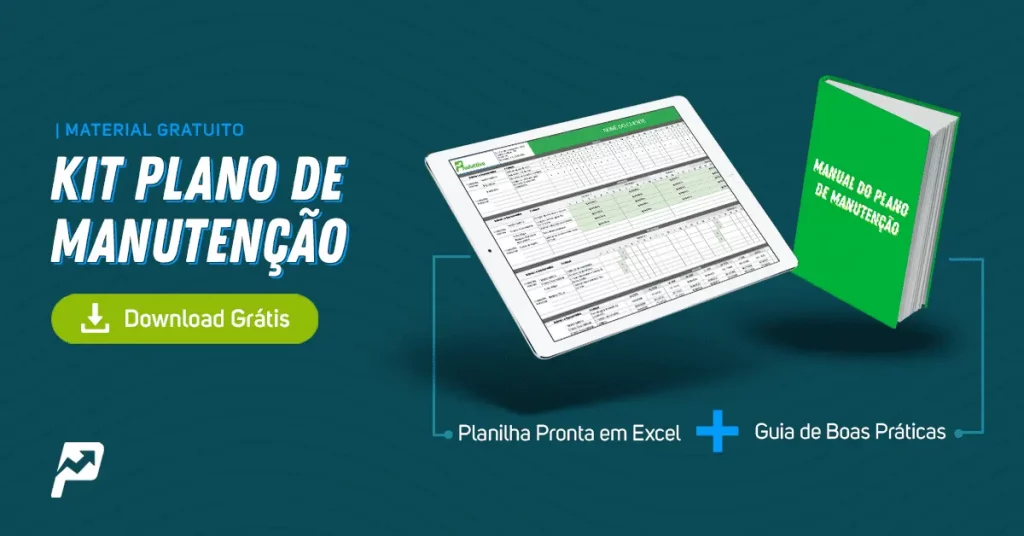
Preparamos também um vídeo que te ensina a configurar a planilha do seu jeito, de acordo com as periodicidades e tipos de inspeções que devem ser desenvolvidas:
Como a inspeção termográfica é feita?
A periodicidade de realização da inspeção termográfica deve ser definida de acordo com o cronograma de manutenção, que deve levar em conta os critérios que mencionamos no tópico anterior.
Depois de definida a recorrência das manutenções, basta utilizar os equipamentos certos e contar com o auxílio de profissionais capacitados para realizar a análise e entender quais variações podem significar um ponto de alerta.
A termografia é simples de ser realizada, ela precisa apenas do termovisor, que é a câmera pela qual a temperatura dos ativos é captada. Assim que as temperaturas são detectadas é necessário realizar o registro em um relatório ou checklist que demonstre quais foram as não conformidades encontradas e quais ações foram aplicadas a partir delas.
Veja abaixo um exemplo de relatório que pode ser utilizado para a sua análise termográfica:
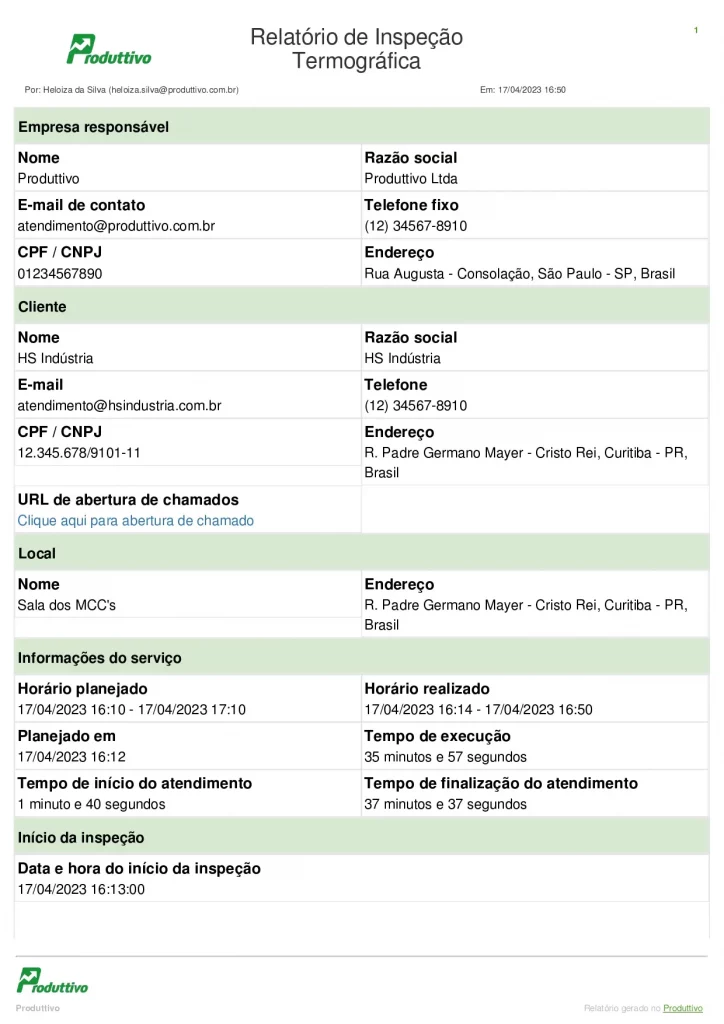
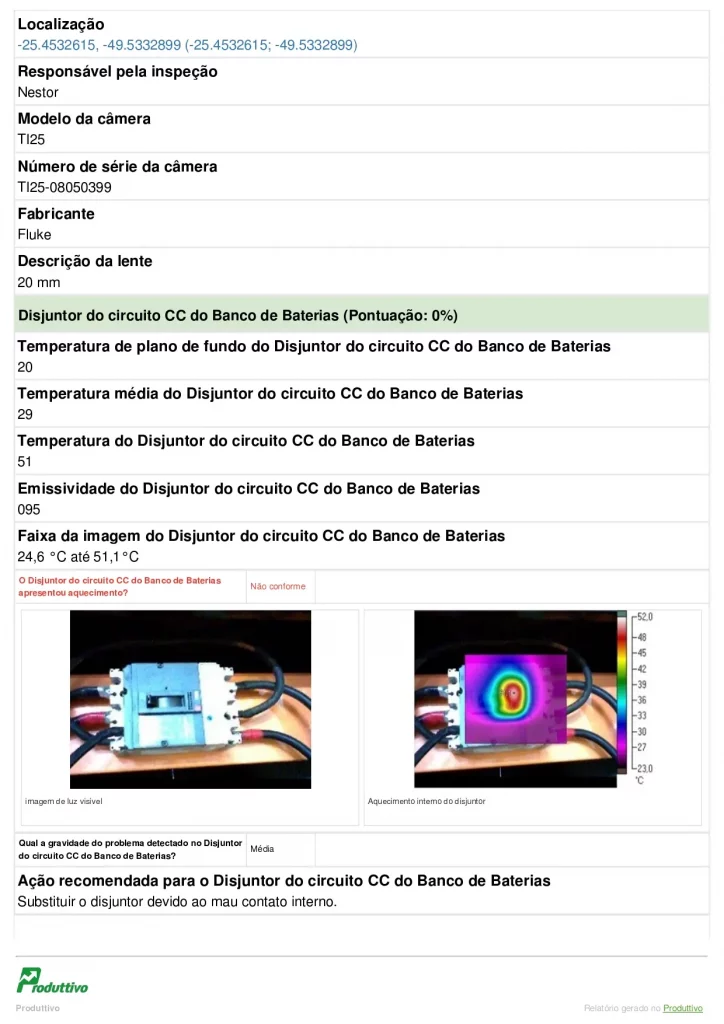
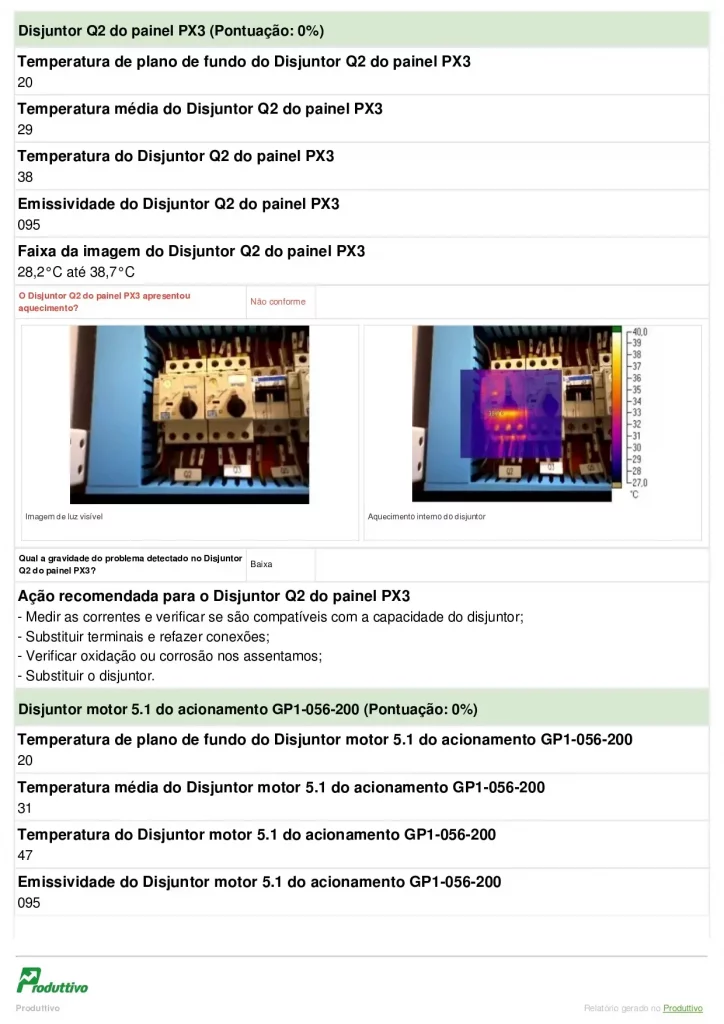
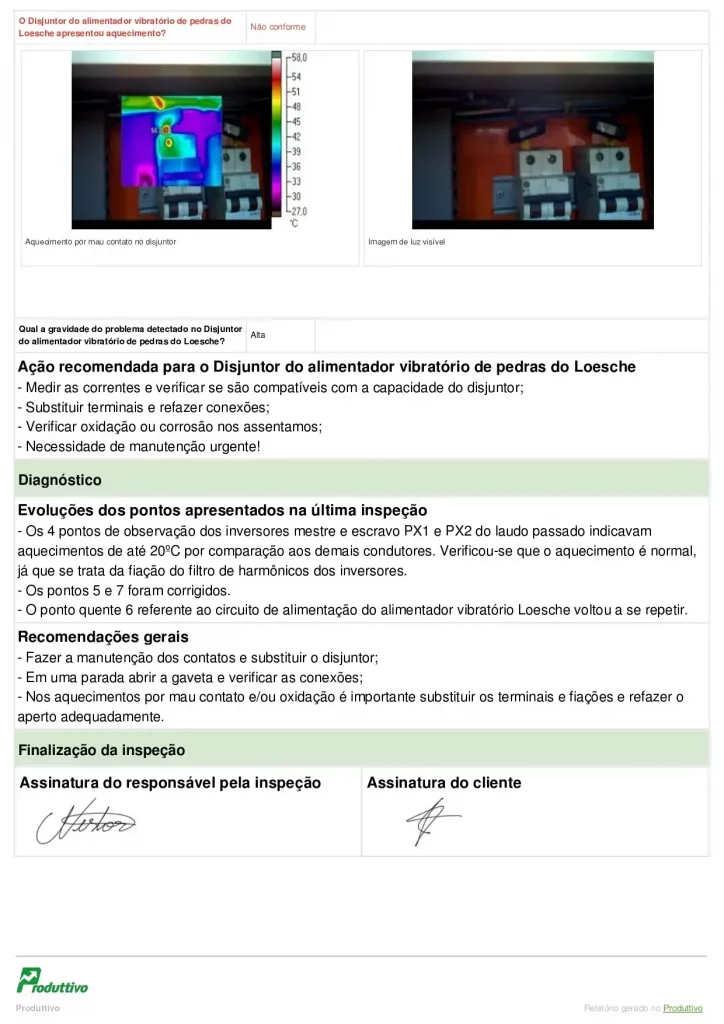
Lembre-se que para que os dados sejam fidedignos é indispensável que eles sejam coletados em condições normais de operação, com cargas e configurações da rotina padrão do setor.
Leia também: Relatório de não conformidade: o que é e como elaborar
Aplicações da termografia
A termografia é uma técnica que pode ser utilizada nos setores industriais, nos sistemas elétricos e em componentes mecânicos. Veja mais sobre a aplicação em cada um:
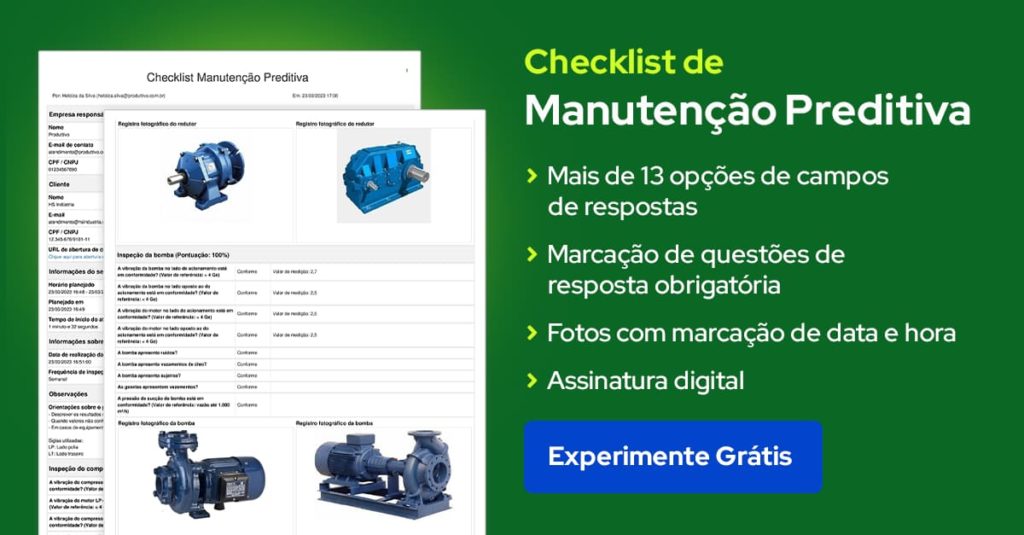
Termografia industrial
A termografia industrial se preocupa em prolongar ao máximo a vida útil dos ativos. Por isso é utilizada para:
- Monitorar o aquecimento de componentes elétricos;
- Identificar falhas em motores elétricos;
- Detectar aquecimento em sistemas rotativos como rolamentos, mancais e acoplamentos;
- Controlar a qualidade dos processos industriais;
- Inspecionar a existência de vazamentos;
- Realizar manutenção preditiva;
- Constatar o desequilíbrio de cargas em um sistema;
- Evitar a ocorrência de incêndios, panes elétricas e sobrecargas de sistemas.
Termografia elétrica
Em sistemas elétricos, a termografia é a principal responsável por identificar anomalias de aquecimento, detectando problemas como:
- Sobrecarga de circuitos;
- Desalinhamento;
- Fuga de correntes em cabos de aterramento;
- Conexões deterioradas ou mal fixadas;
- Obstruções em trocadores de calor;
- Desequilíbrio de tensão e corrente;
- Alto consumo de energia;
- Superaquecimento;
- Falta de isolamento térmico;
- Conexões soltas;
- Entre outros.
Leia também: Laudo técnico elétrico: o que é, como fazer e modelo pronto
Termografia mecânica
Já a termografia mecânica é capaz de identificar falhas, perdas térmicas, desalinhamento, entupimento e corrosão em componentes importantes para o funcionamento dos equipamentos, como:
- Acoplamentos;
- Rolamentos;
- Mancais;
- Motores;
- Selos mecânicos.
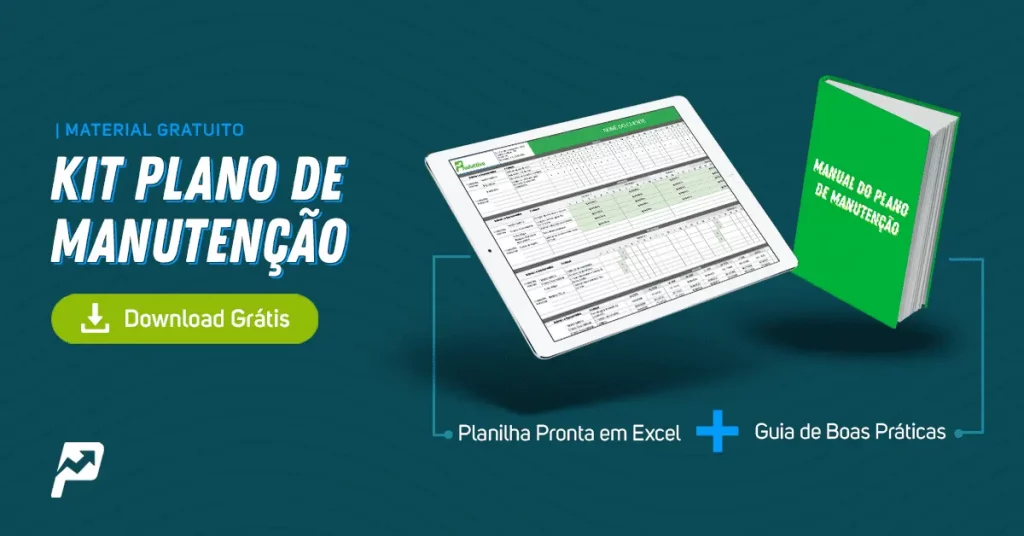
Quais são os equipamentos usados na análise termográfica?
O principal equipamento utilizado na termografia é o termômetro infravermelho, que será o responsável por medir a temperatura dos ativos. Ele pode ser encontrado em três formatos diferentes:
- Termômetro infravermelho spot: Indicado para ser utilizado em ativos de difícil acesso ou em equipamentos que operam sob condições extremas. É usado para medir a temperatura de um ponto específico da superfície.
- Sistemas de scanner infravermelho: Muito utilizado em fábricas com transportadores ou processos de uma planta fabril, pois apresentam uma área de varredura maior.
- Câmeras de imagem térmica infravermelhas: É o equipamento com tecnologia mais avançada. Pode realizar a medição de temperatura em vários pontos de uma grande área e criar imagens bidimensionais.
Quais são os benefícios da inspeção termográfica?
A inspeção termográfica preserva o funcionamento dos ativos e com isso melhora o seu desempenho e produtividade, o que reflete em benefícios para toda a operação. Veja alguns deles:
- Redução da necessidade de manutenção corretivas emergenciais;
- Diminuição do consumo de energia elétrica;
- Aumento de vida útil dos ativos e das instalações;
- Aumento na produtividade da indústria;
- Redução no estoque de peças sobressalentes;
- Aumento de segurança;
- Redução dos riscos de explosões, incêndios e falhas elétricas em sistemas;
- Redução dos custos de manutenção;
- Manutenções planejadas que acabam com paradas inesperadas de produção;
- Melhora na tomada de decisões;
- Redução de reincidência de falhas;
- Melhora nos indicadores de MTBF e Disponibilidade;
- Redução de falhas e defeitos;
- Redução de hora homem para manutenções preventivas e corretivas;
- Elimina a necessidade de desmontagens de equipamentos para inspeção;
- Cumprimento de normas regulamentadoras e normas técnicas.
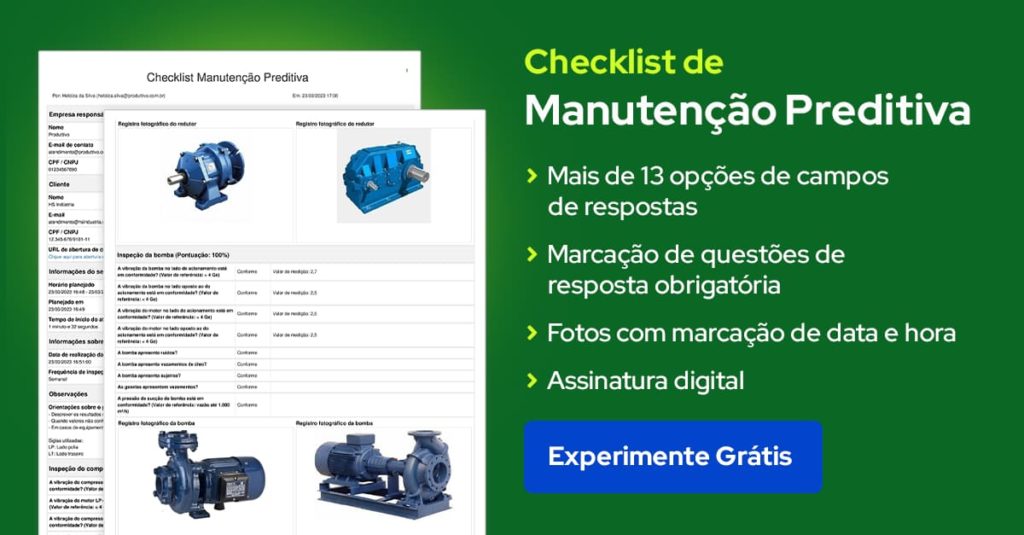
Como implementar a termografia na gestão da manutenção?
A termografia aplicada na gestão da manutenção deve vir acompanhada de estratégia. Por isso, é preciso antes de tudo identificar quais ativos devem receber esse tipo de manutenção, priorizando os ativos mais críticos.
Em seguida você deve considerar os seguintes pontos:
- Depois de listarmos os ativos que passarão pela termografia, é preciso definir qual a melhor periodicidade para a realização da inspeção e os parâmetros que devem nortear as análises. Quais temperaturas são aceitáveis? Quais temperaturas representam um ponto de atenção?
- Crie ordens de serviço e checklists bem roteirizados, com todas as instruções necessárias para a realização do serviço, incluindo os parâmetros de análise que foram definidos no passo anterior;
- Os dados coletados durante a inspeção devem ser todos documentos nos checklists e por meio desses registros as análises e decisões estratégicas serão tomadas;
- Para que a análise seja mais completa, una os dados obtidos a partir da termografia com outras análises preditivas, como a análise de vibração, a análise de óleo e a de ultrassom;
- Planos de ações devem ser sempre programados a partir dos relatórios de manutenção e, se necessário, uma corretiva programada deve ser agendada;
- Sempre que houver necessidade de parar algum maquinário, programe com antecedência para que a parada gere menos impactos na produção;
- Guarde o histórico de todos os relatórios, ordens de serviço e checklists produzidos.
Exemplo de relatório termografia
O relatório de termografia serve para reunir todas as informações coletadas durante a inspeção, criando um histórico das principais não conformidades detectadas e servindo como comprovação dos serviços prestados.
É comum que o relatório apresente informações como: dados gerais da empresa, do cliente e dos ativos inspecionados; checklist de conformidade e registros fotográficos da inspeção.
Para facilitar a produção desse tipo de documento existem aplicativos, como o Produttivo, que digitalizam e automatizam a produção de relatórios. No app é possível:
- Cadastrar informações da empresa, dos clientes e dos equipamentos que são inseridos automaticamente no relatório final sem precisar de preenchimento a cada nova inspeção;
- Tirar fotos com marcação de data, hora e localização GPS;
- Configurar os relatórios para gerarem alertas com base nas não conformidades encontradas;
- Configurar o formulários com mais de 13 tipos de campo de resposta (seleção única, seleção múltipla, texto, números, etc);
- Realizar o preenchimento em campos de texto através do recurso de comando por voz;
- Colher assinaturas digitais diretamente da tela do celular ou tablet dos técnicos;
- E muito mais!
Veja abaixo um exemplo de relatório de termografia gerado no Produttivo:
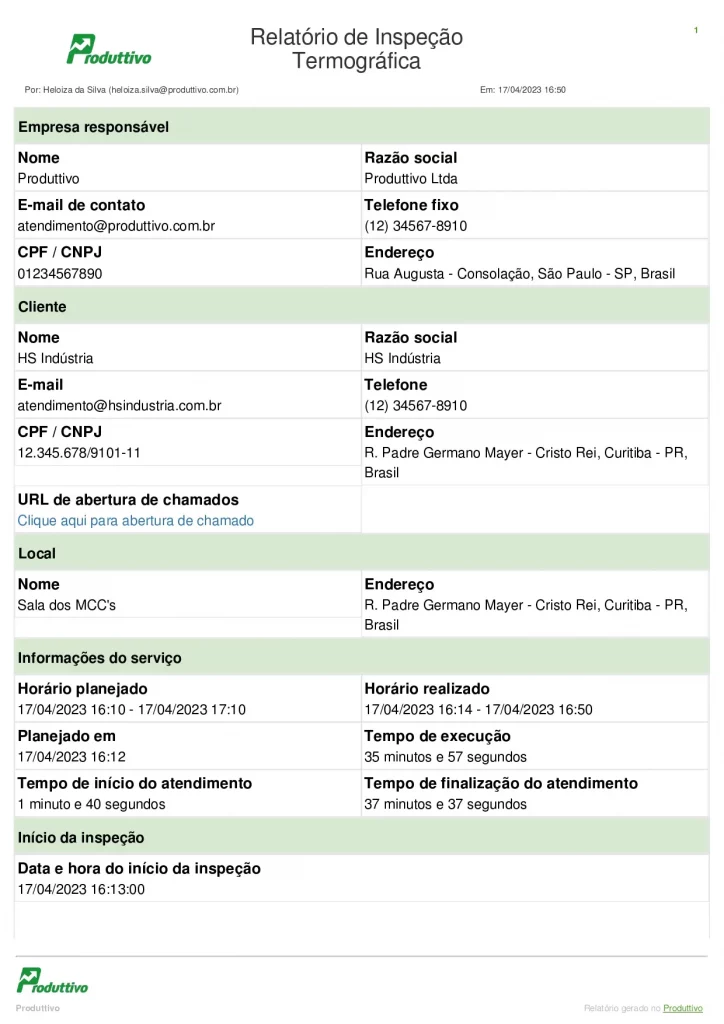
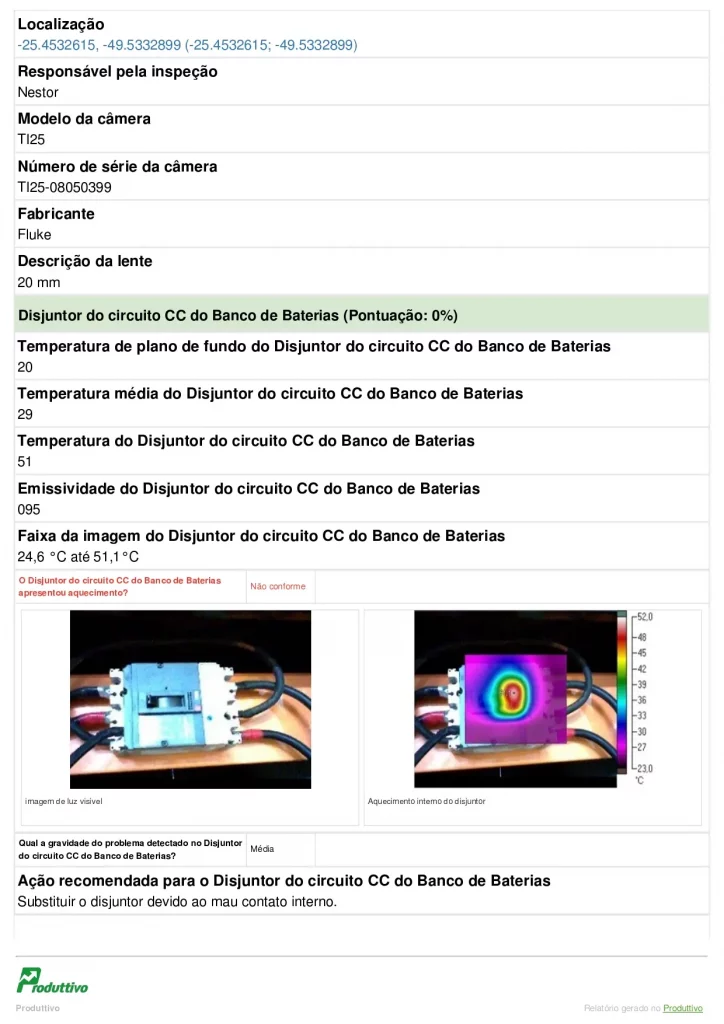
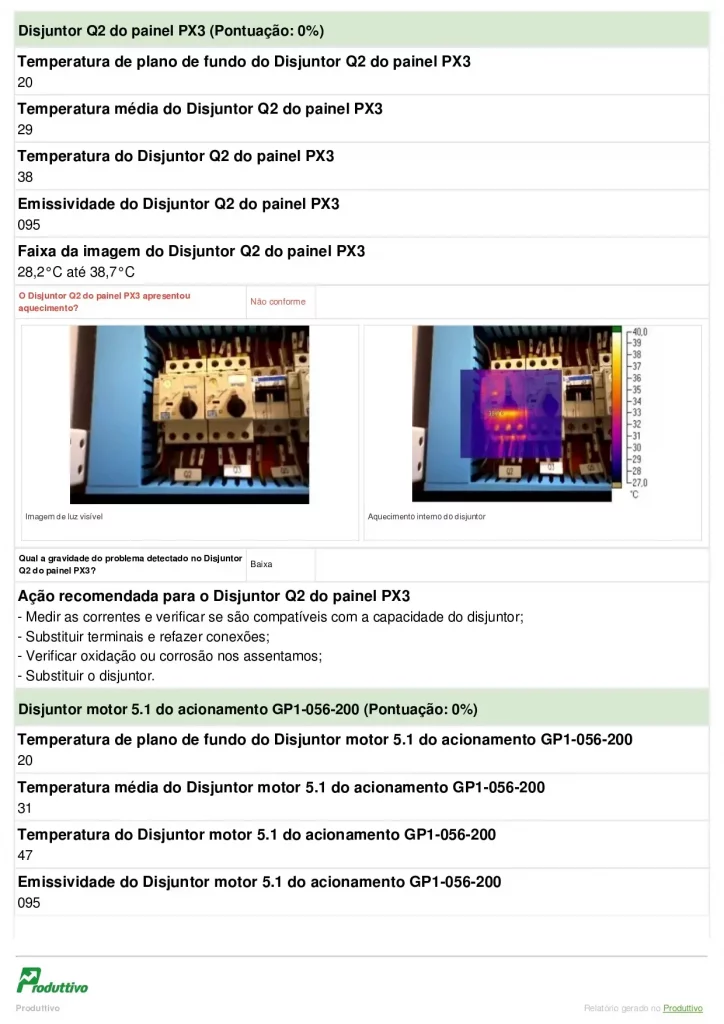
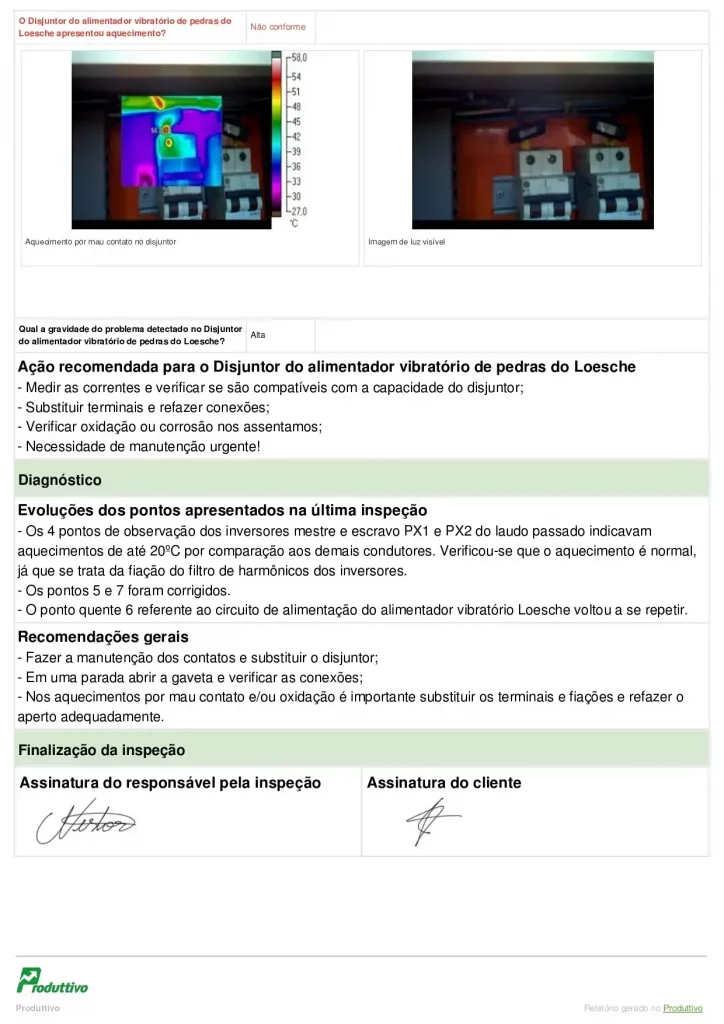
É possível personalizar o seu próprio modelo, inserindo suas próprias questões e personalizando o relatório com a logo e as cores da empresa.
Além disso, o Produttivo oferece recursos que otimizam e melhoram toda a operação:
- Agendamento manual ou automático de manutenções conforme os cronogramas de manutenção;
- Painel web com controle das atividades em andamento e atrasadas;
- Página para recebimento de solicitações de serviço via abertura de chamados;
- Envio de pesquisa de satisfação após a conclusão de um serviço;
- Acompanhamento de indicadores de operação;
- E muito mais!
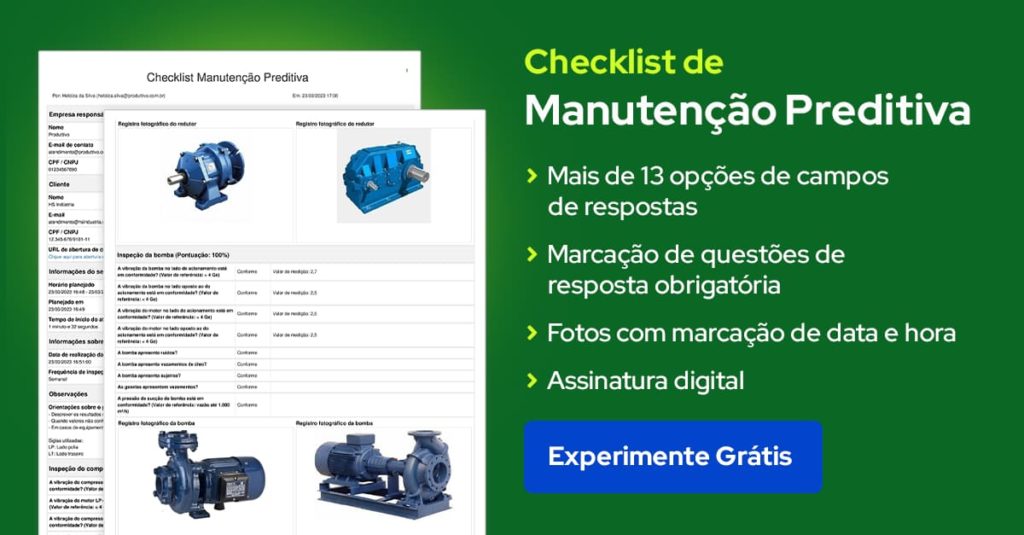
Teste grátis por 15 dias e veja como o Produttivo pode te ajudar a ganhar mais agilidade nas suas manutenções.
{ “@context”: “https://schema.org”, “@type”: “FAQPage”, “mainEntity”: [{ “@type”: “Question”, “name”: “O que é termografia?”, “acceptedAnswer”: { “@type”: “Answer”, “text”: “A termografia é uma forma de inspeção que compõe a manutenção preditiva e serve para avaliar as condições e o estado dos ativos, com base na temperatura que eles apresentam.” } },{ “@type”: “Question”, “name”: “Que tipos de problemas podem ser identificados com a termografia?”, “acceptedAnswer”: { “@type”: “Answer”, “text”: “- Corrosão;
- Entupimentos;
- Mau contato em fiações;
- Sobrecarga de circuitos;
- Oxidação dos elementos da máquina;
- Desgaste de componentes;
- Desgastes de rolamentos;
- Desalinhamento de eixos.
- Prolongar a eficiência operacional de sistemas elétricos;
- Tornar a gestão de ativos mais estratégica;
- Identificar anormalidades térmicas;
- Evidenciar desgastes em fases iniciais;
- Aumentar a confiabilidade dos ativos;
- Aumentar a segurança das instalações;
- Evitar acidentes com risco de incêndio.
- Motores;
- Geradores;
- Transformadores;
- Conectores;
- Disjuntores;
- Fusíveis;
- Chaves seccionadas;
- Linhas de transmissão;
- Rolamentos;
- Mancais;
- Equipamentos e sistemas elétricos;
- Inspeções prediais de umidade, telhado e perda de energia;
- Imagens químicas;
- Níveis de gás e líquidos;
- Vazamentos e falhas dentro de ferramentas, tanques e paredes;
- Prevenção contra incêndios, panes elétricas e sobrecargas de sistema.
- Alterações de temperatura de equipamentos elétricos e mecânicos que estejam em desconformidade com os parâmetros apresentados;
- Interferências na iluminação quando equipamentos são acionados;
- Mudanças de layout para a instalação de novos equipamentos;
- Variações de energia elétrica;
- Aumento no consumo de energia elétrica;
- Queda de rendimento em ritmos normais de operação;
- Vibração acentuada;
- Odores de isolamento ou encapsulamento queimados de fios e cabos.
- Monitorar o aquecimento de componentes elétricos;
- Identificar falhas em motores elétricos;
- Detectar aquecimento em sistemas rotativos como rolamentos, mancais e acoplamentos;
- Controlar a qualidade dos processos industriais;
- Inspecionar a existência de vazamentos;
- Realizar manutenção preditiva;
- Constatar o desequilíbrio de cargas em um sistema;
- Evitar a ocorrência de incêndios, panes elétricas e sobrecargas de sistemas.
- Sobrecarga de circuitos;
- Desalinhamento;
- Fuga de correntes em cabos de aterramento;
- Conexões deterioradas ou mal fixadas;
- Obstruções em trocadores de calor;
- Desequilíbrio de tensão e corrente;
- Alto consumo de energia;
- Superaquecimento;
- Falta de isolamento térmico;
- Conexões soltas;
- Entre outros.
- Acoplamentos;
- Rolamentos;
- Mancais;
- Motores;
- Selos mecânicos.
- Termômetro infravermelho spot: Indicado para ser utilizado em ativos de difícil acesso ou em equipamentos que operam sob condições extremas. É usado para medir a temperatura de um ponto específico da superfície.
- Sistemas de scanner infravermelho: Muito utilizado em fábricas com transportadores ou processos de uma planta fabril, pois apresentam uma área de varredura maior.
- Câmeras de imagem térmica infravermelhas: É o equipamento com tecnologia mais avançada. Pode realizar a medição de temperatura em vários pontos de uma grande área e criar imagens bidimensionais.
- Redução da necessidade de manutenção corretivas emergenciais;
- Diminuição do consumo de energia elétrica;
- Aumento de vida útil dos ativos e das instalações;
- Aumento na produtividade da indústria;
- Redução no estoque de peças sobressalentes;
- Aumento de segurança;
- Redução dos riscos de explosões, incêndios e falhas elétricas em sistemas;
- Redução dos custos de manutenção;
- Manutenções planejadas que acabam com paradas inesperadas de produção;
- Melhora na tomada de decisões;
- Redução de reincidência de falhas;
- Melhora nos indicadores de MTBF e Disponibilidade;
- Redução de falhas e defeitos;
- Redução de hora homem para manutenções preventivas e corretivas;
- Elimina a necessidade de desmontagens de equipamentos para inspeção;
- Cumprimento de normas regulamentadoras e normas técnicas.
- 1. Depois de listarmos os ativos que passarão pela termografia, é preciso definir qual a melhor periodicidade para a realização da inspeção e os parâmetros que devem nortear as análises. Quais temperaturas são aceitáveis? Quais temperaturas representam um ponto de atenção?
- 2. Crie ordens de serviço e checklists bem roteirizados, com todas as instruções necessárias para a realização do serviço, incluindo os parâmetros de análise que foram definidos no passo anterior;
- 3. Os dados coletados durante a inspeção devem ser todos documentos nos checklists e por meio desses registros as análises e decisões estratégicas serão tomadas;
- 4. Para que a análise seja mais completa, una os dados obtidos a partir da termografia com outras análises preditivas, como a análise de vibração, a análise de óleo e a de ultrassom;
- 5. Planos de ações devem ser sempre programados a partir dos relatórios de manutenção e, se necessário, uma corretiva programada deve ser agendada;
- 6. Sempre que houver necessidade de parar algum maquinário, programe com antecedência para que a parada gere menos impactos na produção;
- 7. Guarde o histórico de todos os relatórios, ordens de serviço e checklists produzidos.