Desenvolvido em 1950 por Taiichi Ohno, engenheiro da Toyota, o método Lean Manufacturing busca reduzir o desperdício em linhas de produção e maximizar os lucros da empresa.
Por isso, também é chamado de manufatura enxuta. Seus princípios incluem identificar o que agrega valor ao cliente, eliminar atividades que não agregam valor, criar um fluxo de produção contínuo e produzir com base na demanda real (produção puxada).
No artigo a seguir, vamos entender melhor os cinco princípios do Lean Manufacturing, quais são os benefícios e como implementar nos negócios. Acompanhe!
Experimente grátis: Software para gestão de ativos e serviços
O que é Lean Manufacturing?
Lean Manufacturing é uma filosofia de gestão voltada para a produção enxuta, que busca aumentar o valor do produto para o cliente, eliminando desperdícios e otimizando processos produtivos.
Seu principal objetivo é aumentar a eficiência da operação e reduzir custos sem comprometer a qualidade do produto final.
Essa abordagem foi popularizada pela Toyota no Japão e hoje é amplamente usada em várias indústrias ao redor do mundo para melhorar produtividade e eficiência.
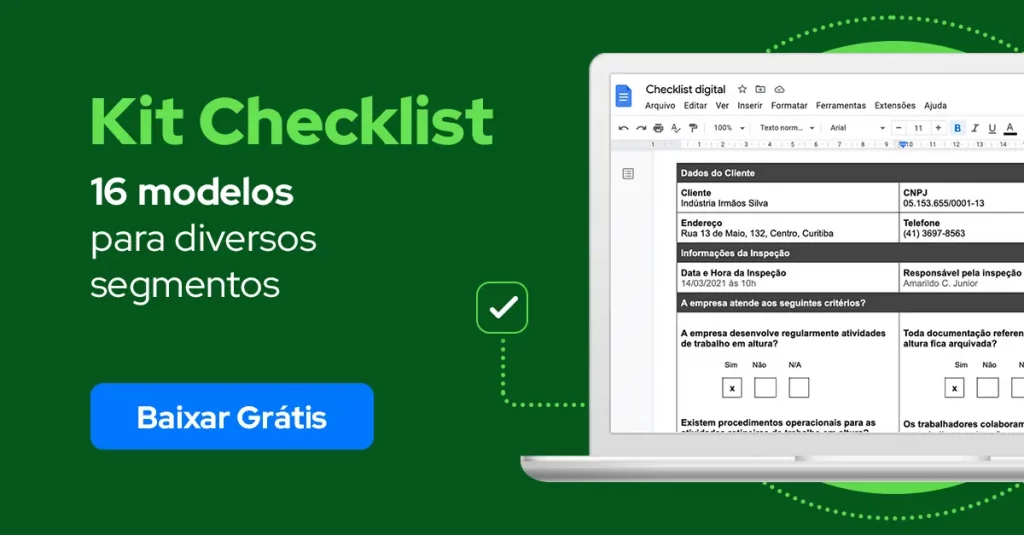
O que é Lean?
Lean é uma filosofia de gestão que busca criar mais valor para o cliente, utilizando menos recursos e eliminando desperdícios nos processos.
O objetivo do Lean é maximizar a eficiência e entregar exatamente o que o cliente precisa, de forma mais rápida e com menos custos. Embora tenha origem na manufatura, o conceito de Lean é amplamente aplicado em diversos setores, como serviços, saúde, TI e até mesmo em projetos de inovação.
Por que o Lean Manufacturing é importante?
O Lean Manufacturing é importante por várias razões, especialmente no contexto industrial e empresarial. Seus benefícios vão além da redução de custos, abrangendo melhorias em eficiência, qualidade e satisfação dos clientes.
Sua principal importância está na melhoria ampla dos processos gerais da empresa, já que o método aborda diferentes etapas da operação e assim busca resultados abrangentes, como melhorar a eficiência operacional, aumentar a qualidade dos produtos e serviços, e oferecer maior valor aos clientes, ao mesmo tempo em que reduz custos e ganha competitividade.
Quais são os 5 princípios do Lean Manufacturing?
Os 5 princípios do Lean Manufacturing são os pilares fundamentais que orientam a aplicação dessa metodologia em processos produtivos. Eles foram estabelecidos para ajudar as empresas a maximizar valor, eliminar desperdícios e melhorar continuamente a operação. Vamos conhecê-los:
Valor
O primeiro passo é entender o que realmente é valor para o cliente. Isso significa identificar o que o cliente está disposto a pagar e focar em entregar exatamente esse valor. Qualquer atividade que não contribua para gerar esse valor é considerada desperdício.
Fluxo de valor
Após definir o valor, o próximo passo é mapear o fluxo de valor, ou seja, todas as atividades e etapas necessárias para criar e entregar o produto ou serviço ao cliente.
O objetivo é identificar e eliminar atividades que não agregam valor, como esperas, movimentações desnecessárias e retrabalhos.
Fluxo contínuo
Com as atividades que não agregam valor eliminadas, é preciso organizar o processo produtivo para que o fluxo seja contínuo e sem interrupções. Isso significa que o produto ou serviço flui de uma etapa para outra sem atrasos, gargalos ou tempos de espera, otimizando o tempo de produção.
Produção puxada
No sistema de produção puxada, a fabricação de produtos é guiada pela demanda do cliente, em vez de ser baseada em previsões ou produção em massa. Assim, a empresa só produz o que é necessário, quando é necessário, minimizando estoques excessivos e superprodução.
Perfeição
O princípio final é a melhoria contínua, ou Kaizen. A busca pela perfeição envolve a revisão e o aprimoramento constante de todos os processos. Mesmo quando o sistema já parece eficiente, sempre há espaço para melhorias, seja na redução de desperdícios, na melhoria da qualidade ou na redução do tempo de ciclo.
Esses princípios formam a base da filosofia Lean e são aplicáveis a qualquer setor, não apenas à manufatura, com o objetivo de criar processos mais enxutos e eficientes.
Quais são os benefícios do Lean Manufacturing?
O Lean Manufacturing traz muitos benefícios para as empresas, já que seu objetivo é aumentar a produtividade como um todo. Vamos entender melhor quais são essas vantagens:
Melhora a eficiência
Um grande benefício do Lean Manufacturing é que ele melhora a eficiência dos processos, já que elimina etapas desnecessárias e otimiza o uso do tempo, elevando a produtividade da empresa.
Reduz o desperdício
Um dos principais objetivos do Lean Manufacturing é eliminar desperdícios, conhecidos como “muda” em japonês. Esses desperdícios incluem superprodução, tempo de espera, movimentação desnecessária, excesso de estoque, defeitos, entre outros.
Ao eliminar essas ineficiências, a empresa pode operar de forma mais econômica, poupando recursos como tempo, matéria-prima e mão de obra.
Além disso, com o princípio da produção, ou seja, ajustada à demanda real, não há produção em massa que pode gerar estoques excedentes.
Aumenta a flexibilidade
O Lean Manufacturing aumenta a flexibilidade das empresas ao permitir que elas se adaptem rapidamente às mudanças na demanda, otimizando recursos e ajustando os processos de produção de maneira ágil conforme necessário.
Dessa forma, a empresa se adapta às tendências de mercado e solicitações dos clientes com rapidez quando preciso.
Melhora a qualidade
A aplicação de Lean Manufacturing ainda reduz erros e defeitos nos produtos, já que cada processo é continuamente aprimorado e controlado para manter a consistência e a qualidade. Isso resulta em menos retrabalho e mais satisfação do cliente.
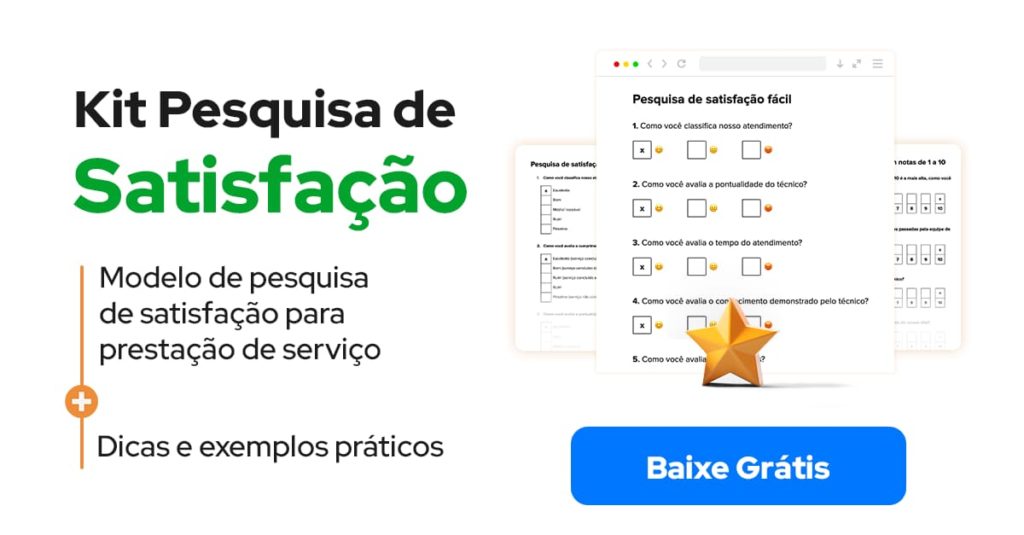
Quais são as fontes de desperdício?
No Lean Manufacturing, as fontes de desperdício, também conhecidas como “muda”, são todas as atividades ou recursos que não agregam valor ao produto ou serviço final. A eliminação desses desperdícios é fundamental para aumentar a eficiência e reduzir custos.
Existem sete fontes principais de desperdício (7 desperdícios do Lean), e uma oitava foi posteriormente adicionada, chamada de desperdício de talento humano. Olha só:
Transporte
O desperdício de transporte é a movimentação desnecessária de materiais, produtos e até informações dentro da fábrica ou ao longo da cadeia de suprimentos. Esse desperdício não agrega valor ao produto e pode causar danos aos materiais, aumentar custos e o tempo de produção.
Estoque
Manter estoque de matérias-primas, componentes ou produtos acabados maior do que o necessário ocupa espaço, imobiliza capital, aumenta os custos de armazenamento e pode levar à obsolescência de produtos, sendo uma fonte de desperdício de recursos.
Movimentação
Assim como o transporte, os movimentos desnecessários de pessoas, como busca de ferramentas, materiais ou instruções, geram desperdício de tempo e esforço. Movimentos ineficazes ou não planejados podem causar fadiga nos trabalhadores e prejudicar a produtividade.
Espera
Já a espera é qualquer tempo em que um recurso (máquinas, pessoas ou material) não está sendo utilizado adequadamente. Esperas ocorrem quando há atrasos entre uma fase e outra do processo, como tempo de inatividade de máquinas ou trabalhadores ociosos aguardando material ou instruções.
Superprodução
Produzir mais do que o necessário ou antes que seja necessário gera excesso de estoque, aumenta o custo de armazenamento e pode resultar em produtos que não serão vendidos ou que ficarão obsoletos.
Processamento excessivo
Outra fonte de desperdício são etapas ou atividades que não são necessárias ou que não agregam valor ao produto. Isso pode incluir retrabalho, inspeções desnecessárias ou uso inadequado de tecnologia, resultando em desperdício de tempo e recursos.
Retrabalho
Produzir produtos com falhas ou erros que requerem retrabalho ou, em casos mais graves, descarte. Defeitos geram desperdício de materiais, tempo e custos adicionais para corrigir os problemas.
Intelectual
Um tipo de desperdício identificado mais recentemente envolve não utilizar de forma adequada as habilidades, capacidades e criatividade dos funcionários. Isso ocorre quando o potencial dos colaboradores não é aproveitado devido a falta de treinamento, oportunidades limitadas para melhorias ou ausência de participação nos processos de decisão.
Eliminar essas fontes de desperdício é a chave para implementar o Lean Manufacturing com sucesso.
Como implementar o Lean Manufacturing?
Implementar o Lean Manufacturing requer uma abordagem estruturada e planejada, envolvendo a empresa inteira em uma transformação cultural e operacional.
A implementação é gradual e depende de um comprometimento organizacional com os princípios do Lean. Separamos um passo a passo que pode te ajudar, confira:
Tenha uma equipe enxuta e multitarefa
Como você já sabe, eliminar o desperdício é uma parte muito importante do método Lean Manufacturing. Ao investir em uma equipe enxuta, o gestor assegura que haja a quantidade necessária de trabalhadores, sem déficit de pessoas, nem excedente.
Para aproveitar o talento da equipe, procure por funcionários que possam executar diferentes tarefas e saibam se adaptar às mudanças.
Diminua o tempo de produção
O desperdício de tempo também pode ser eliminado, e isso pode ser feito com a redução do tempo de produção. Descarte processos redundantes e procure por oportunidades para diminuir o tempo das atividades, seja investindo na automatização ou terceirizando serviços.
Controle a qualidade
A gestão da qualidade é essencial para a implementação do Lean Manufacturing, uma vez que a excelência nos produtos e serviços contribui para a redução do desperdício e a satisfação do cliente.
Aposte em auditorias internas, faça inspeções regulares e acompanhe seus indicadores para assegurar a qualidade da sua empresa.
Produza com base em projeções realistas
Como você já sabe, o Lean Manufacturing se baseia na manufatura enxuta, e isso inclui um estoque adequado, sem excedentes que levam ao desperdício. Portanto, ao planejar sua produção, baseie-se em projeções realistas que considerem uma demanda provável, em vez de cenários que podem nunca se concretizar.
Se necessário, vá ajustando as projeções à medida que for observando resultados e mudanças nos padrões de consumo.
Como a tecnologia pode ajudar o Lean Manufacturing?
A tecnologia está diretamente relacionada com o sucesso do Lean Manufacturing, já que alguns recursos podem ser usados para automatizar processos com precisão e controle, atendendo aos princípios do método.
Vamos conhecer algumas maneiras que a tecnologia pode ajudar:
Automação
A automação de tarefas repetitivas ou complexas pode reduzir erros, aumentar a produtividade e liberar os funcionários para se concentrarem em atividades de maior valor agregado.
Por exemplo: ao automatizar o preenchimento do relatório de qualidade, sua equipe tem mais tempo para se dedicar ao problema em si, em vez de se preocupar com detalhes superficiais do documento.
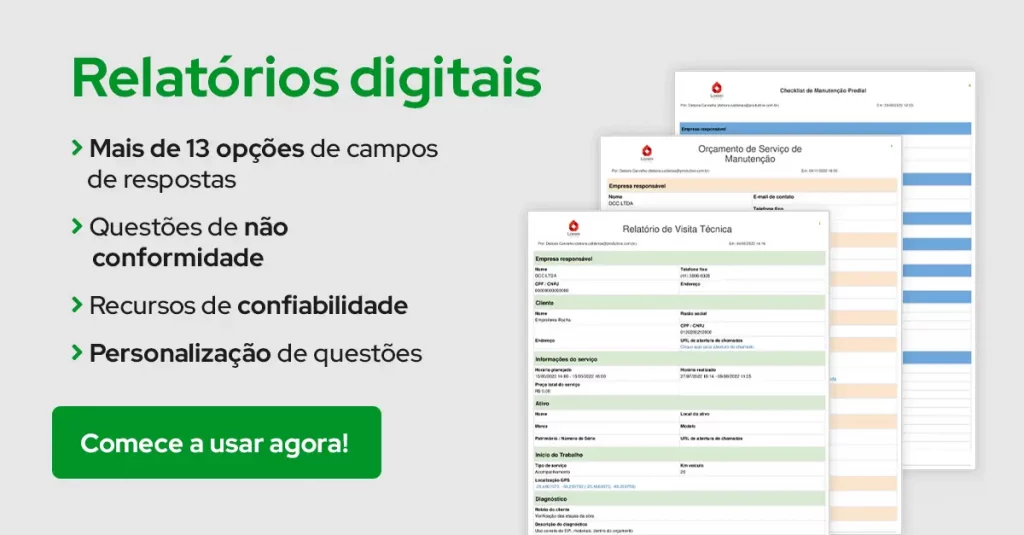
IoT e sensores
A IoT (Internet of Things, ou internet das coisas) permite que máquinas, dispositivos e sensores se conectem e compartilhem dados em tempo real.
No Lean Manufacturing, isso facilita o monitoramento de máquinas e processos de produção, ajudando a identificar gargalos, falhas e oportunidades de melhoria antes que se tornem problemas maiores.
Sensores IoT também possibilitam uma manutenção preditiva mais eficiente, reduzindo o tempo de inatividade das máquinas.
Análise de dados
A análise de grandes volumes de dados pode fornecer insights detalhados sobre o desempenho de processos e identificar áreas de desperdício que não são visíveis a olho nu.
O Produttivo conta com um dashboard de indicadores que reúne automaticamente os principais dados da sua empresa, coletando-os a partir dos relatórios preenchidos e transformando-os em gráficos fáceis de entender e analisar.
Olha só:
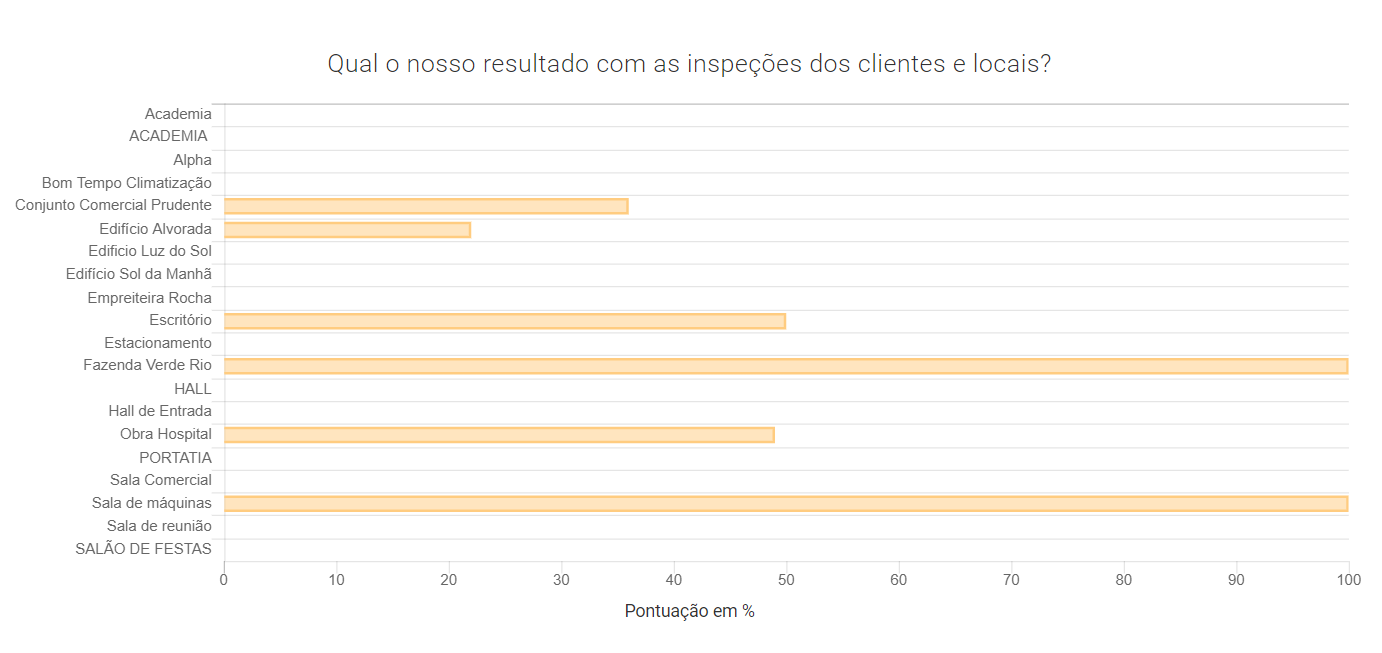
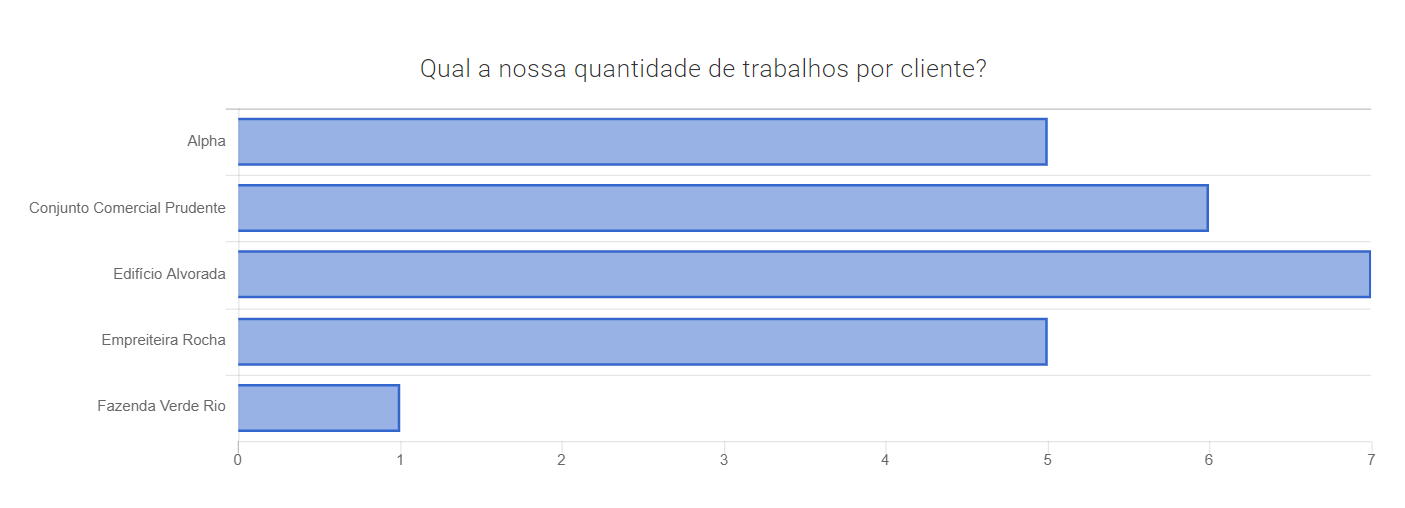
Experimente grátis: Sistema para gestão com dashboard automático de indicadores
Sistemas de Gestão Integrada
Softwares de SGI integram todas as operações da empresa em um único software, permitindo a gestão centralizada de pessoas, serviços, ativos e dados em tempo real.
No Lean Manufacturing, um SGI pode otimizar o fluxo de trabalho, controlar estoques, gerenciar pedidos e garantir que a produção seja ajustada à demanda real, evitando excessos e desperdícios.
Sistemas de Controle de Produção (MES)
Um Manufacturing Execution System (MES) monitora e controla o processo de produção em tempo real, rastreando desde a movimentação de materiais até o desempenho das máquinas e a eficiência dos trabalhadores. Isso permite uma produção mais enxuta, com maior visibilidade sobre o fluxo de trabalho e ajustes rápidos em caso de desvios.
Sistemas de qualidade automatizados
O uso de câmeras e sensores inteligentes pode ajudar a detectar falhas ou defeitos automaticamente durante o processo de produção, garantindo que os produtos atendam aos padrões de qualidade sem a necessidade de inspeções manuais demoradas. Sistemas de qualidade automatizados reduzem a incidência de defeitos e retrabalhos, promovendo a eficiência e a satisfação do cliente.
Manutenção preditiva com Inteligência Artificial
A combinação de inteligência artificial (IA) e dados em tempo real de sensores de máquinas permite a implementação de manutenção preditiva, que antecipa falhas de equipamentos com base em padrões de desempenho. Isso reduz o tempo de inatividade não planejado e aumenta a disponibilidade das máquinas, evitando interrupções no fluxo contínuo de produção.
O Produttivo é um software digital para gestão de serviços, ativos e equipes externas. O sistema conta com recursos como:
- Modelos digitais de relatórios, checklists e outros formulários;
- Plano de atividades automático para planejar serviços recorrentes com antecedência;
- Calendário da equipe;
- Dashboard de dados e indicadores;
- Pesquisa de satisfação enviada automaticamente;
- E muito mais!
Faça um teste grátis e experimente todos os recursos do Produttivo sem pagar nada!