A Manutenção Produtiva Total (TPM) é um tipo de manutenção que envolve toda a equipe no cuidado com equipamentos e na qualidade dos produtos.
Essa estratégia diminui falhas inesperadas nas máquinas, acidentes, descumprimento de prazos e aumento inesperado de custos.
Criada no Japão, a TPM é referência no mundo todo por conta dos resultados excelentes a partir de pequenas mudanças de comportamento.
Neste artigo, você vai entender o que é, como funciona e quais os benefícios de aplicar esse modelo de manutenção na sua empresa.
Boa leitura! 😉
Garanta o controle automático de manutenção na sua empresa: Teste grátis software de manutenção
- O que é Manutenção Produtiva Total?
- Quais são os 4 objetivos da Manutenção Produtiva Total?
- Como a Manutenção Produtiva Total evoluiu ao longo do tempo?
- Quais são os 8 pilares da Manutenção Produtiva Total?
- Quais são as vantagens da manutenção produtiva total?
- O que é necessário para implementar a Manutenção Produtiva Total?
- Em quais empresas a Manutenção Produtiva Total é recomendável?
- Como a Manutenção Produtiva Total ajuda a reduzir avarias em máquinas e equipamentos?
- Como implementar a Manutenção Produtiva Total na sua empresa?
- Como a tecnologia pode ajudar na Manutenção Produtiva Total?
O que é Manutenção Produtiva Total?
A Manutenção Produtiva Total é um um sistema abrangente de ações e práticas com o propósito de minimizar gargalos de processo.
Apesar de ser um tipo de manutenção, como a preventiva ou corretiva, a TPM se destaca por envolver todas as equipes e a gestão da empresa, além da área responsável pela manutenção.
O intuito de englobar todos os funcionários é aumentar a produtividade da empresa como um todo.
Esse tipo de manutenção não se resume apenas em manter o bom estado de equipamentos e prolongar sua vida útil. Ela se preocupa também com a qualidade final dos produtos e com a redução de acidentes no ambiente de trabalho.
Quais são os 4 objetivos da Manutenção Produtiva Total?
Como você já viu, a Manutenção Produtiva Total vai além da simples conservação de máquinas.
Seu foco está em tornar toda a produção mais eficiente, segura e colaborativa, garantindo o máximo desempenho da empresa.
Para isso, a metodologia se baseia em quatro objetivos principais:
- Maximizar a eficiência dos equipamentos: um dos intuitos da Manutenção Produtiva Total é eliminar ou reduzir ao máximo falhas de ativos, paradas inesperadas na produção e desperdício de produtos ou matéria-prima, garantindo o melhor desempenho possível de todo o ciclo produtivo;
- Envolver todos os funcionários: diferente de outros tipos de manutenção, a TPM incentiva a participação de todos da empresa na busca por melhorias, o que cria um senso de identidade e de cuidado com os ativos;
- Aumentar a segurança no trabalho: ao tornar práticas preventivas e inspeções constantes na empresa e incentivar a participação dos trabalhadores, a Manutenção Produtiva Total torna o ambiente mais seguro.
- Melhorar a qualidade dos produtos: a aliança entre aparelhos em bom estado, equipe integrada e ambiente de trabalho seguro não poderia ser diferente. O resultado é um serviço ou produto final de excelência e a satisfação do seu cliente.
Como a Manutenção Produtiva Total evoluiu ao longo do tempo?
Desde que foi criada, na década de 70, a TPM passou por mudanças caracterizadas por quatro diferentes fases. Veja:
- Primeira geração: A prioridade era aumentar ao máximo a eficiência dos equipamentos, utilizando a política de zero falha;
- Segunda geração: A partir daqui, o foco deixou de ser somente a eliminação de falhas nos ativos. Foram introduzidos também as outras cinco das seis grandes perdas quando falamos de equipamentos: além das falhas, também foram feitos esforços para evitar ajustes inesperados, pequenas paradas, redução da velocidade de produção, defeitos no processo e perdas antes da produção propriamente dita;
- Terceira geração: O foco deixou de ser somente nos ativos. A eficiência dos processos e a participação de todos os colaboradores na manutenção começaram a ser discutidas;
- Quarta geração: Atualmente, a Manutenção Produtiva Total é caracterizada pela integração com outras metodologias de gestão, como por exemplo o Ciclo PDCA e o Lean Manufacturing, com o intuito de alcançar a excelência operacional.
Quais são os 8 pilares da Manutenção Produtiva Total?
A manutenção produtiva total tem uma meta ousada: zerar paradas inesperadas, defeitos nos produtos e acidentes. Logo, precisa ser bem fundamentada para funcionar.
Por isso, existem os 8 pilares básicos que permitem a implementação da Manutenção Produtiva Total e garantem a longa duração dos processos necessários.
1. Manutenção da qualidade
Seguindo os princípios da Manutenção Produtiva Total, a organização da empresa é fundamental para identificar problemas na linha de produção e nos processos internos.
É necessário estabelecer parâmetros consistentes e atualizados de controle de qualidade, permitindo a atuação direta na causa raiz de problemas recorrentes.
As etapas desse processo incluem:
- Levantamento da situação da qualidade – Como está o controle de qualidade na sua empresa?
- Análise das causas – Quais as possíveis causas para qualidade abaixo do esperado nos produtos ou serviços que a sua empresa oferece?
- Eliminação das causas – Como é possível eliminar os problemas de qualidade nos seus produtos ou serviços?
- Padronização dos procedimentos – Estabelecimento de regras em toda a cadeia produtiva.
2. Manutenção Planejada
Planejar as manutenções também é um passo da Manutenção Produtiva Total. A equipe responsável pelo processo de manutenção faz um levantamento do que vai precisar ser reparado ou inspecionado.
O acompanhamento é detalhado e devem ser elaborados relatórios para implementação das melhorias, escolhendo também o tipo de manutenção mais adequada.
As principais etapas da manutenção planejada são:
- Análise da diferença entre condições básicas e condição atual;
- Melhorias nos métodos atuais;
- Desenvolvimento dos padrões de manutenções;
- Medidas para estender a vida útil do equipamento e controlar as inconveniências;
- Melhoria da eficiência da inspeção e do diagnóstico;
- Diagnóstico geral do equipamento;
- Uso adequado do equipamento até o seu limite;
- Uso de calendário de manutenção, evitando esquecimentos.
3. Manutenção Autônoma
É importante que as empresas designem pessoas específicas para pequenas ações de manutenção, como limpeza e lubrificação.
Esses pequenos grupos de pessoas são chamados de grupos autônomos na Manutenção Produtiva Total. A ideia é que esses grupos cuidem da tarefa pela qual ficaram responsáveis, identifiquem as perdas e implementem melhorias.
Essa etapa só é possível com o aumento da capacitação das pessoas ou melhoria da qualidade do time.
4. Melhorias específicas
É o pilar da Manutenção Produtiva Total que ajuda a eliminar as grandes perdas da empresa.
A metodologia consiste em identificar a maior perda de um equipamento ou de um processo, seja ele produtivo ou administrativo, e atacá-la sistematicamente até que a perda seja zerada.
O trabalho deve ser realizado em grupo, com o apoio de especialistas quando necessário. Cada caso deve ser estudado e as soluções devem ser personalizadas.
Aqui estão algumas etapas que podem ser incluídas nesse processo:
- Redução das grandes paradas que geram ineficiências;
- Melhoria da eficiência global dos equipamentos (OEE);
- Melhoria da produtividade do trabalho;
- Promoção da produção sem interferência humana;
- Redução de custo;
- Aumento da disponibilidade no período noturno.
Leia mais: O que são MTBF e MTTR e quais as principais diferenças?
5. Educação e Treinamento
O capital humano é fundamental em todas as empresas e a Manutenção Produtiva Total reconhece isso.
Para fazer a implementação da automatização, é preciso que os funcionários saibam de todos os processos e dominem as tecnologias. Por isso, ofereça capacitação e treinamento.
Sabemos que o conhecimento e a compreensão da metodologia TPM é essencial para o funcionamento de todos os seus pilares.
Sendo assim, as etapas de implementação da capacitação e treinamento são:
- Determinação do perfil ideal dos operadores e mantenedores;
- Avaliação da situação atual;
- Elaboração do plano de treinamento para operadores e mantenedores;
- Implantação do plano;
- Determinação de um sistema de avaliação do aprendizado;
- Criação de um ambiente de autodesenvolvimento;
- Avaliação das atividades e estudos de métodos para atividades futuras.
6. Controle de equipamentos
O controle de equipamentos é de extrema importância, pois o início de todo novo ciclo da Manutenção Produtiva Total precisa ser baseado em informações confiáveis.
Aqui, analisamos minuciosamente tudo o que é necessário para uma instalação, uma troca de peça ou o que for realizado durante a manutenção.
Com esse levantamento, os processos de manutenção se tornam mais fáceis e eficientes. Busque registrar todas essas informações, utilizar os manuais dos equipamentos e conversar com a equipe responsável.
7. Áreas administrativas
Aqui também é prevista a eliminação dos erros e perdas, mas por parte do setor administrativo.
Pode-se considerar que um escritório nada mais é do que uma fábrica de informações, onde entram insumos (informações de entrada), que são processados e transformados em um produto (informações de saída).
Dessa forma, esse pilar da Manutenção Produtiva Total é responsável por conduzir o programa e formar os times de melhorias para atuar nas resoluções dos problemas, utilizando a Metodologia de Análise e Solução de Problemas (MASP).
Leia mais: O que é e como executar a Análise de Criticidade na manutenção?
8. Segurança, higiene e meio ambiente
Garantir a segurança, a saúde e a preservação da natureza e dos ambientes de trabalho é o objetivo deste pilar da TPM.
Assim, acidentes que possam afetar a integridade física dos colaboradores ou a conservação das empresas são evitados e o bem-estar é mantido.
Separamos algumas possíveis fases para implantação durante este pilar:
- Identificações de perigos, aspectos, impactos e riscos;
- Eliminação de perigos e aspectos;
- Estabelecimento do controle de impactos e riscos;
- Treinamento em segurança, saúde e meio ambiente;
- Inspeções de segurança;
- Padronização;
- Gestão autônoma.
A escolha de procedimentos ecologicamente corretos também é um objetivo deste pilar, que preza pela preservação do meio ambiente e o bem estar da comunidade.
Quais são as vantagens da manutenção produtiva total?
A Manutenção Produtiva Total traz inúmeros benefícios, como: produtividade, segurança, eficiência nos processos, aumento da autonomia, proatividade e ainda deixa os funcionários mais independentes.
Além disso, existem outras vantagens:
- Redução de paradas repentinas;
- Eliminação dos defeitos e anomalias;
- Satisfação dos clientes;
- Economia dos custos de produção;
- Aumento de sugestões de melhoria partindo de colaboradores;
- Autogestão da equipe;
- Ambiente de trabalho mais organizado e limpo.
O que é necessário para implementar a Manutenção Produtiva Total?
Agora que você já conhece os 8 pilares da TPM, precisa saber o que é indispensável para a sua aplicação: a organização. Sem esse fator, é muito mais difícil identificar problemas.
Uma boa possibilidade para tornar sua empresa mais estruturada é aplicar o programa 5S, uma metodologia japonesa que possibilita a organização que vai levar, posteriormente, às melhorias.
Confira o que cada um dos 5S significam:
- Seiri (Uso): senso de utilização, ou seja, identificar o que de fato é utilizado durante o trabalho e descartar, doar ou vender tudo o que não tiver utilidade;
- Seiton (organização): nesta etapa, o que não foi descartado deve ser categorizado e um lugar específico deve ser destinado para guardar cada coisa. A equipe deve ter conhecimento sobre isso e sempre alocar os materiais e ferramentas no local correto;
- Seiso (limpeza): toda a equipe e responsáveis devem identificar e eliminar rotinas que causem bagunças e sujeiras no ambiente de trabalho, mantendo a saúde mental e física dos trabalhadores e prevenindo acidentes;
- Seiketsu (padronização): a ideia é padronizar todos os conceitos anteriores, de modo que eles sejam fáceis de entender e seguir e conhecidos por todos os funcionários;
- Shitsuke (disciplina): aqui os funcionários devem repetir continuamente e cumprindo o protocolo todos os hábitos que garantem um ambiente de trabalho produtivo sem o estímulo da diretoria.
Após a implantação do 5s, tanto a equipe quanto a empresa estarão mais aptas a implantar a Manutenção Produtiva Total.
Em quais empresas a Manutenção Produtiva Total é recomendável?
A TPM é recomendável para empresas de diversos segmentos em algumas situações específicas. Veja:
- Alto uso de máquinas e equipamentos: Quanto mais a produção depende de máquinas, maior o impacto da Manutenção Produtiva Total na redução de falhas e paradas.
- Custo significativo com manutenção corretiva: Se a empresa gasta muito com reparos emergenciais, a TPM ajuda a reduzir esses custos com a manutenção planejada.
- Baixa eficiência operacional: Se há perdas frequentes de produtividade por paradas não planejadas, retrabalho ou falhas na qualidade, a TPM pode reverter esse cenário.
- Cultura de melhoria contínua: A TPM exige envolvimento de toda a equipe, então empresas que incentivam treinamentos, participação dos funcionários e metodologias como Kaizen ou Ciclo PDCA têm mais chances de sucesso.
- Compromisso com segurança e qualidade: Se a empresa busca reduzir acidentes e desperdícios, a TPM contribui para um ambiente mais seguro e uma produção mais estável.
Como a Manutenção Produtiva Total ajuda a reduzir avarias em máquinas e equipamentos?
Existem 6 tipos principais de perdas comuns dentro das indústrias, as quais a TPM se propõe a eliminar, de forma a aumentar a produtividade e lucratividade. Veja:
- Quebras: quando um equipamento quebra, além do prejuízo para conserto, existe também o “lucro cessante”, como é chamado o prejuízo que a empresa leva durante o tempo em que não pôde produzir. Para eliminar esse problema, a TPM sugere a realização de medições de indicadores em tempo real dos equipamentos.
- Setup: aqui a perda está relacionada a quanto tempo a equipe leva para configurar uma máquina para executar uma tarefa. É muito comum quando o equipamento fabrica mais de um tipo de produto. Um pilar da Manutenção Produtiva Total que ajuda nesse contexto é o treinamento dos colaboradores, para que eles conheçam bem o produto, os ativos e suas funções.
- Tempo ocioso: este é o tempo em que as máquinas ficam paradas entre as trocas de peças. Por isso, deve-se investir em treinamento e capacitação para que esse tempo ocioso seja reduzido e também planejar as manutenções de maneira estratégica.
- Baixa velocidade: quando um equipamento passa a operar em baixa velocidade, a empresa produz menos do que deveria. Neste sentido, a manutenção preditiva pode ajudar, identificando rapidamente quais máquinas estão em velocidade reduzida e intervir.
- Baixa qualidade: aqui o foco é reduzir custos com retrabalho, aplicando o pilar de manutenção de qualidade e garantindo que as máquinas operem com qualidade, sem danificar produtos.
- Perdas de startup: aqui os problemas ocorrem, normalmente, na aquisição de matéria-prima, quando se identificam falhas e defeitos antes mesmo do item entrar no processo de produção. Assim, a escolha de bons fornecedores e uma comunicação bem próxima pode ajudar a reduzir o problema.
Como implementar a Manutenção Produtiva Total na sua empresa?
Para implementar a TPM manutenção, existem algumas fases que são necessárias. Abaixo, vamos te apresentar um passo a passo para que você consiga implementar em sua empresa.
Preparação
Os gestores devem definir o objetivo do programa TPM e todas as políticas e metas do programa. Também devem ser indicadas quais serão as responsabilidades de cada uma das pessoas que participarão do processo.
Além disso, é interessante mapear os ativos e localizar todas as matérias-primas. Basicamente, deve ser feita uma análise interna de recursos.
Por exemplo: há mão de obra especializada para um determinado projeto? Se não, como vamos começar essa capacitação? Ou então: todas as nossas máquinas estão em boas condições para realizar o trabalho? Se não, vamos aplicar um plano de manutenção?
A partir disso, a ideia é que seja formulado um plano de ação para apresentar para os trabalhadores.
É importante basear-se em fatos, mas não fechar a ideia totalmente, para ouvir as opiniões de quem tem acesso às diversas fases do processo de fabricação diariamente.
Introdução
Nesta etapa deve ocorrer um treinamento introdutório para os funcionários sobre os pilares da Manutenção Produtiva Total. O plano desenvolvido na fase de preparação é divulgado, abrindo espaço para ideias e soluções da equipe.
É importante que fique claro quais são os objetivos, os planos de ação e como os cronogramas de manutenção, por exemplo, foram desenvolvidos.
Implementação
Na fase de implementação, todas as ações de melhoria são colocadas em prática. Por isso, os gestores devem escolher qual será a área piloto da implantação, ou seja, por onde a empresa deve começar para entender se o processo faz sentido ou não.
Depois que a área piloto estiver 100%, a equipe deve partir para outros setores.
Não esqueça de registrar todo o processo para ter comparativos durante as análises posteriores. É assim que você, gestor, vai entender o que deve ser mantido, melhorado ou eliminado do processo.
Utilizar ferramentas que irão otimizar esse acompanhamento é fundamental: o plano de manutenção, por exemplo, é um documento que define periodicidades e auxilia a ter os históricos das manutenções necessárias.
Consolidação
Por último, todos os processos devem ser padronizados e se tornar uma cultura dentro da empresa.
A equipe deve prezar pelo cuidado com os equipamentos, ajustando qualquer etapa ou procedimento que não esteja otimizando a produção. O acompanhamento próximo das equipes também é fundamental para entender como tudo está funcionando.
Como a tecnologia pode ajudar na Manutenção Produtiva Total?
A tecnologia é aliada das empresas que buscam otimizar a manutenção. O acompanhamento de máquinas e equipamentos, quando feito de forma manual, leva muito tempo da equipe.
Além disso, se não há padronização das ordens de serviço e da execução da manutenção, falhas podem ocorrer.

Ao utilizar um sistema de manutenção como o Produttivo, o gestor conta com:
- Planos automáticos de manutenção, evitando atrasos nos serviços;
- Acompanhamento de dados e gráficos sobre não conformidades;
- O técnico realiza o atendimento e preenchimento de checklists via aplicativo, emitindo relatórios de comprovação em segundos, logo após a finalização do serviço;
- Caso o técnico identifique problemas durante a manutenção, pode marcar a não conformidade no relatório, gerando um alerta ao gestor. Isso oferece mais agilidade para reparos;
- É possível emitir laudos, inspeções, relatórios técnicos, relatórios fotográficos e muitos outros documentos, sem necessidade de internet;
- O preenchimento via aplicativo conta com vários recursos, como campo para foto, localização GPS em tempo real, cálculo automático de peças e materiais. Com isso, papéis e planilhas são desnecessários, concentrando os preenchimentos no sistema do Produttivo.
O planejamento de manutenção e serviços é feito automaticamente, a partir da periodicidade cadastrada no app, e tem integração total com a agenda dos técnicos.
Com ele, você dá adeus aos esquecimentos, garantindo a saúde dos ativos, e economiza o tempo que gastaria gerenciando todas as demandas. Veja um exemplo:
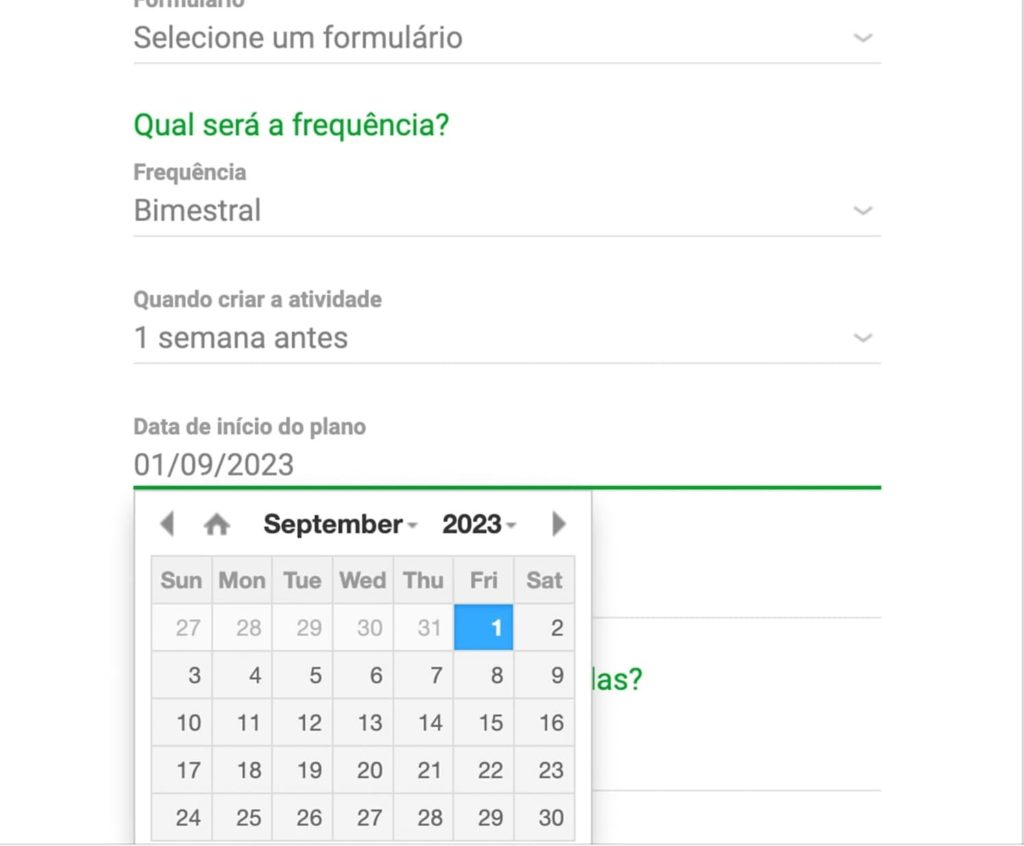
Você pode testar as funcionalidades sem pagar nada. Faça agora seu cadastro e tenha direito a 15 dias grátis, ou fale com um de nossos consultores para saber mais sobre planos e condições!